Efficiency is always the key to the photovoltaic industry, but as the efficiency of the cell increases, the increase in current in the series circuit brings about greater resistance power loss, which makes the development of the cell module encounter a bottleneck. How to reduce the loss becomes the key to improve the efficiency, thus the half-sheet module technology was born.
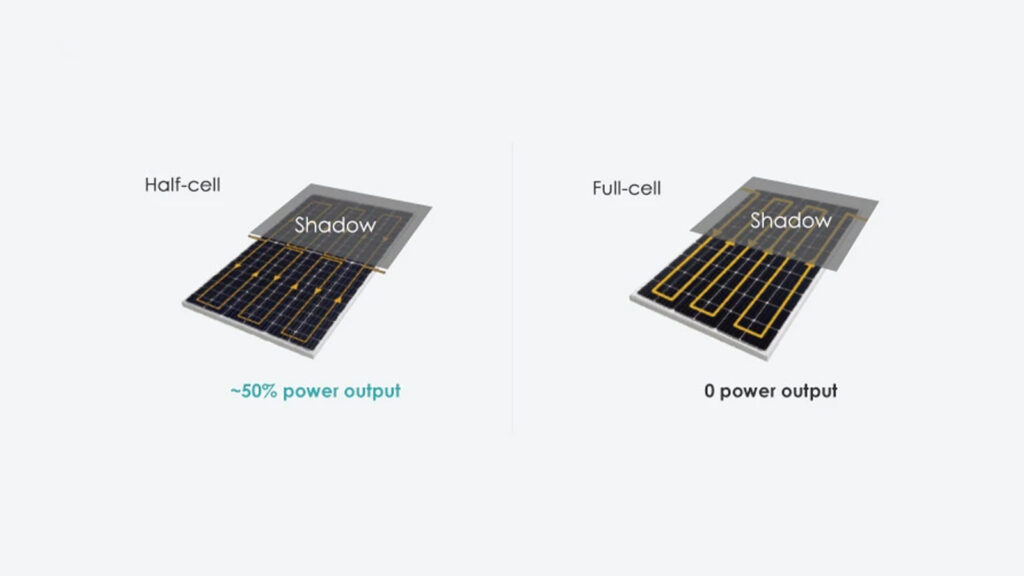
Laser cutting technology
Half cell technology generally uses laser cutting to cut the cell into two identical halves along the direction perpendicular to the main grid line of the cell, and then weld them in series. While keeping the output voltage unchanged, the current is changed to one-half of the original, significantly reducing the power loss.
From the appearance, I believe you can find the difference between the half cell modules. Due to the series-parallel structure design, the module is divided into two in the longitudinal direction, which is equivalent to two small modules connected in parallel, and the current is led out from the back of the module through a sink strip in the middle, and the current is channeled into the power-using equipment through a three-part junction box.
The main cutting equipment used in the photovoltaic industry are diamond cutting machines and laser scribing machines. Due to the higher efficiency of laser cutting and the emergence of “non-destructive cutting” technology, laser scribing technology has become mainstream.
Conventional laser scribing technology is dominated by laser with mechanical breaking technology, which has a higher damage rate than non-destructive cutting technology and is susceptible to cutting dust.
Non-destructive cutting technology increases the yield rate to more than 99%. The principle is to use the laser in conjunction with a cooling system to fracture the cell under thermal tension and perform rapid cooling so that the fracture expands steadily along the cutting direction.
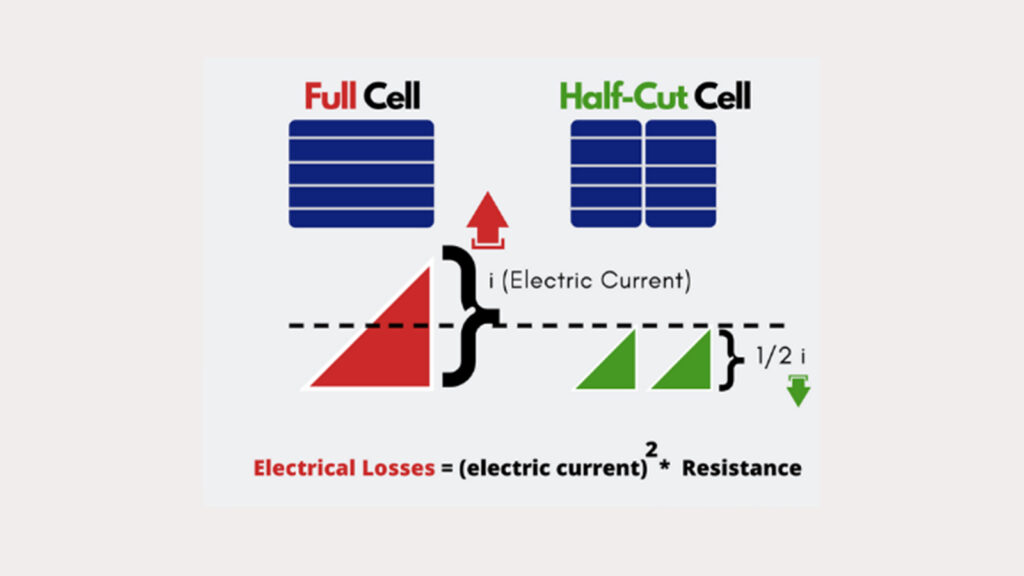
Half-sheet cutting operation flow
In general, the half cell cutting is divided into 4 steps of loading, cutting, inspection and collection, which requires 1-2 people to complete the operation.
When cutting cells, parameters such as laser power and scribing speed need to be set according to the size, thickness, warpage and capacity requirements of the cells. After the setting is completed, the operator will feed the sorted cells into the machine and transport the cells to the laser cutting table through the robot arm and conveyor belt.
To ensure the stability of the cells during the cutting process, the table is equipped with air holes, and the cells are adsorbed and fixed on the console when the vacuum pump is turned on. The cut cells will be inspected and the qualified and unqualified cells will be processed separately. Half cell cutting is non-contact processing, which prevents cell damage and contamination.
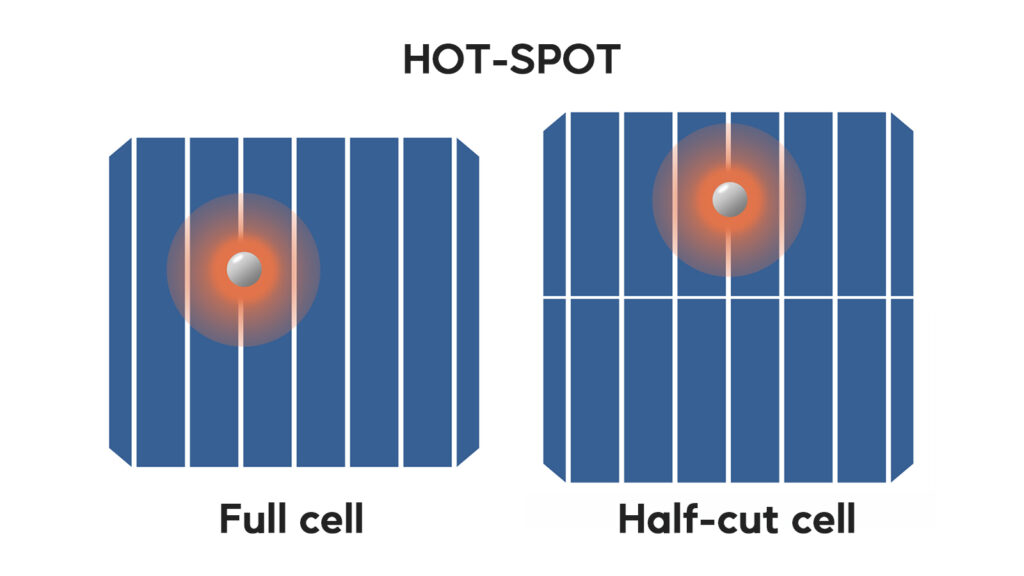
What are the advantages of half cell?
1. Smaller cells reduce the consumption of resistance and improve the efficiency of photoelectric conversion.
2. Smaller shading shading area reduces the risk of hot spot due to shading solar cell module heating.
3. Series-parallel circuit design to reduce module current mismatch loss due to inconsistent cell performance.
4. The gap area between cells is increased to allow secondary reflection of light within the module and improve optical utilization.
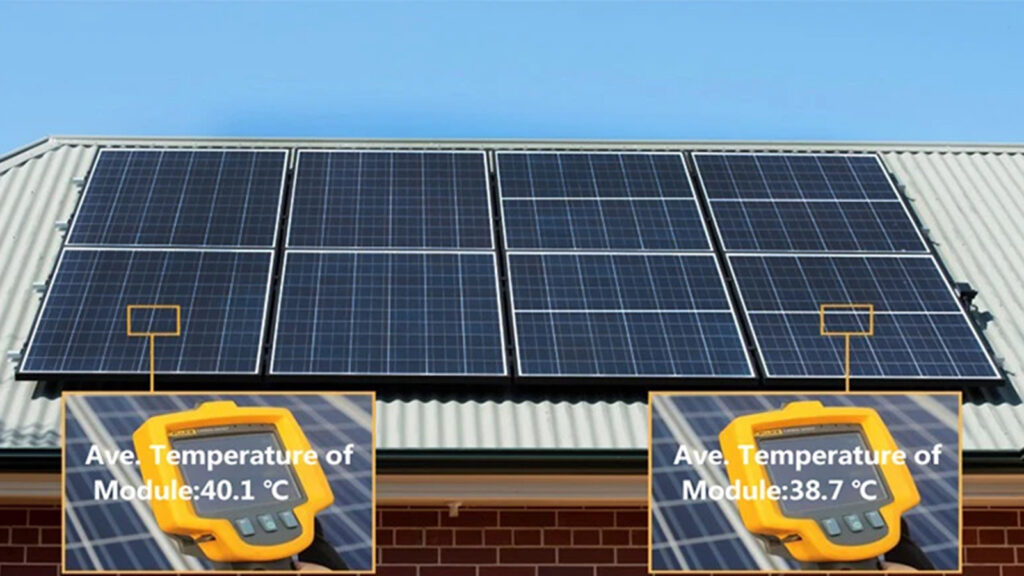
Maysun Solar, as a PV module manufacturer with 15 years of professional experience, also has a variety of half-sheet modules, interested parties can click the button below for product details, or contact us via WhatsApp.