Introduction
In the global photovoltaic market, crystalline silicon solar cells dominate a substantial share. However, as the industry rapidly evolves, reducing costs and improving efficiency have become primary challenges for these cells. Traditional solar cells use a significant amount of silver paste to create busbars and fingers, which not only increases costs but also blocks some sunlight, limiting the power generation efficiency. To address these issues, 0 Busbar (0BB) technology was developed. This technology eliminates busbars, reduces the use of silver paste, and increases the light-receiving area of the cells, significantly enhancing the power generation efficiency and economic viability of photovoltaic modules.
Table of Contents
The Birth of 0 Busbar (0BB) Technology
When sunlight hits a photovoltaic cell, it generates electricity through the photovoltaic effect. However, this electricity needs to be collected and extracted via grid lines for human use. Traditional photovoltaic cells use silver-based grid lines, divided into fingers and busbars. Fingers are thinner, while busbars are thicker. Electricity is collected by the fingers, transferred to the busbars, and then conducted out via copper ribbons.
Since the first practical monocrystalline silicon solar cell was developed by Bell Labs in 1954, the number and width of grid lines on photovoltaic cells have continuously evolved. From 2BB (two busbars) to MBB (multi-busbars) and SMBB (super multi-busbars), increasing the number of busbars has made each busbar narrower, saving on silver paste and reducing costs. More busbars also shorten the current path in the fingers, reducing power loss and increasing power output.
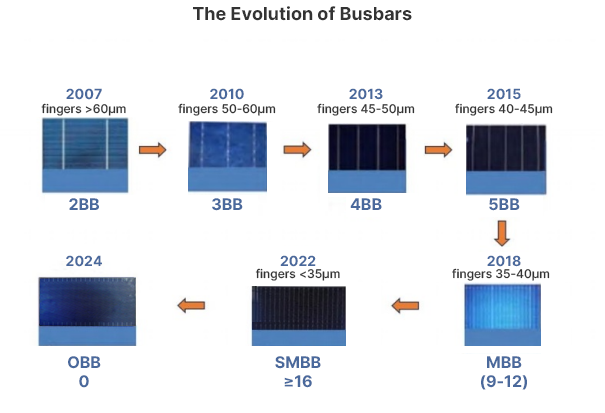
Despite the widespread application of MBB and SMBB technologies in the industry, some researchers proposed a novel approach: removing the busbars and directly connecting the fingers to the ribbons via solder points. This concept is the essence of 0 Busbar (0BB) technology.
0BB technology enhances the light-receiving area of the cells by eliminating busbars, reducing the use of silver paste, lowering costs, and improving power generation efficiency.
Advantages of 0 Busbar (0BB) Technology
1.Power Increase:
Removing the busbars reduces shading, thereby increasing power output. The denser distribution of solder points in 0BB technology shortens the current path in the fingers, reducing power loss and enhancing power generation. Additionally, the larger surface area on photovoltaic cells, while maintaining the popular mounting standard of up to 210 mm cell size, results in higher power output from a single PV panel.
2.Cost Reduction:
Traditional grid lines are made from silver paste, which accounts for approximately 35% of the non-silicon cost of photovoltaic cells. The rising price of silver has exerted pressure on photovoltaic cell manufacturing. By eliminating the main busbar, 0BB technology reduces the cost of silver paste, thereby lowering the overall cost of photovoltaic cells.
According to data from the Silver Institute, global photovoltaic silver demand reached 6,017 tons in 2023, a year-on-year increase of 64%. In 2024, global photovoltaic silver demand is expected to rise by 20% to 7,217 tons. However, the persistently high silver prices have posed significant challenges to the photovoltaic cell manufacturing industry. Domestic silver prices have increased by over 30% since October of last year.
0BB technology, by removing the main busbar, can lower non-silicon costs, thus reducing the overall cost of photovoltaic cells. Among the current three technological routes, HJT (Heterojunction Technology) has the highest silver paste cost and the most urgent need for cost reduction. Specifically, the current mass-produced PERC (Passivated Emitter and Rear Cell) silver paste cost is 0.06 yuan per watt, TOPCon (Tunnel Oxide Passivated Contact) silver paste cost is 0.07 yuan per watt, while the cost for HJT with 210 size 15BB silver paste is as high as 0.15 yuan per watt. In the future, with the mass production of 20BB, the HJT silver paste cost is expected to decrease to 0.12 yuan per watt.
After adopting 0BB technology, the silver paste cost for PERC can be reduced to 0.03 yuan per watt, TOPCon to 0.01 yuan per watt, and HJT to 0.04-0.06 yuan per watt. Additionally, if 0BB technology is combined with 30% silver-coated copper paste, the final silver paste cost for HJT is expected to drop to 0.03-0.04 yuan per watt.
3.Enhanced Efficiency:
0BB technology decreases electrical resistance within the solar cell, resulting in more efficient electron movement and increased energy conversion efficiency. This leads to higher energy output from the same amount of sunlight, making 0BB solar cells more productive.
4.Improved Shading Tolerance:
The presence of multiple thin connections in 0BB cells creates multiple pathways for electrical current, reducing the risk of power loss due to partial shading. This is particularly advantageous in installations where shading from objects like trees or buildings can affect performance.
5.Reduced Hotspots:
0BB technology evenly distributes electrical current over the cell surface, minimizing the occurrence of hotspots caused by high resistance. This helps prevent efficiency drops and long-term degradation of the cell.
6.Higher Quality:
With smaller and more numerous solder points, stress distribution in the cells is more uniform, reducing cell breakage, gridline breakage, and microcracks, thereby improving production yield. Additionally, the uniform stress distribution allows 0BB technology to use thinner silicon wafers, which can be as thin as 100μm according to experts.
By incorporating these advantages, 0BB technology significantly enhances the performance, durability, and efficiency of photovoltaic modules, positioning it as a key advancement in the solar energy industry.
Disadvantages of 0 Busbar (0BB) Technology
Despite its significant advantages, 0BB technology still faces several challenges, including ensuring welding consistency and efficiency testing. The most pressing issue is reliability. The fingers and solder points are a combination of silver and glass, making the structure loose and unstable. Since the solder ribbons are made of copper, the differing properties of silver and copper make it difficult to achieve a solid weld, leading to potential detachment and affecting the normal operation of photovoltaic cells.
0 Busbar (0BB) Solar Cells Interconnection
1.First Method: SmartWire Connection Technology
The core component of SmartWire Connection Technology is the copper wire composite film. This film is composed of an electrically insulating, optically transparent layer, an adhesive layer on the film’s surface, and multiple parallel copper wires (tabbing ribbons) embedded within the adhesive layer. These copper wires, bonded to the film via the adhesive, protrude with a low-melting-point alloy coating.
During the lamination process, the copper wire composite film connects the solar cells in series. The film is overlaid with an encapsulation film, backsheet, or glass, creating a stable electrical connection between the tabbing ribbons and the grid during the heating process.
The copper wire composite film is laminated on the surfaces of adjacent solar cells to form a series connection. Unlike conventional solar cell packaging, this method uses a new stringer machine to place the copper wire composite film on both the front and back surfaces of two cells, enabling their series connection. Once interconnected, the cells are arranged and stacked. Under specific lamination temperatures and pressures, the copper wires and solar cell grids are pressed together to form an ohmic contact.
2.Second Method: Dispensation
(1)Dispensing: Apply adhesive droplets on the surface of each solar cell.
(2)Tabbing: Evenly space multiple tabbing ribbons perpendicular to the grid lines on each solar cell.
(3)Fixing: Use UV light to cure the adhesive, bonding each tabbing ribbon to its corresponding solar cell, ensuring direct contact with the surface grid lines.
(4)Lamination: Heat and laminate the solar cell assembly to form alloy connections between the tabbing ribbons and grid lines.
This method differs from traditional stringing in two main ways:
(1)Dispensing: Adhesive droplets bond the tabbing ribbons to the solar cells, allowing for series connection and immobilization of the ribbons for subsequent module encapsulation.
(2)Alloying through Lamination: Achieve ohmic contact during the lamination process.
Advantages of this method include simple equipment and high stability. However, potential shadows during EL testing under the tabbing ribbons and insufficient bonding strength between the ribbons and solar cells are disadvantages.
3.Third Method: Soldering Dispensation
(1)Soldering: Use infrared heating to melt the surface of the solder ribbon, creating a preliminary connection with the solar cell surface and grid lines.
(2)Dispensing: Apply adhesive droplets at specified locations on the soldered solar cell-ribbon assembly. The number of adhesive droplets is carefully controlled to balance process complexity and bonding strength requirements. Typically, 3-8 rows of adhesive droplets are applied based on shadowing area and mechanical performance needs.
(3)Curing: Solidify the adhesive droplets on the front side of the soldered cell string. Transfer the cell string to the next station, flip it under controlled temperature conditions, and apply and cure adhesive droplets on the backside, forming the final cell string.
Compared to adhesive bonding, this method involves a preliminary soldering step followed by adhesive application for reinforcement. The initial connection between the solder ribbon and the grid lines is established through infrared heating. Adhesive is then applied and cured to enhance the stability of the solder ribbon-cell connection.
Advantages of this method include strong bonding between the solder ribbon and the solar cell, reducing the risk of ribbon detachment. However, there is a risk of grid breakage during soldering, and the dispensing process requires high precision, making it challenging and relatively slow.
By implementing 0BB technology in HJT solar cells, the photovoltaic industry can achieve significant cost reductions and efficiency improvements, driving the future of solar energy innovation.
Market Prospects for 0 Busbar (0BB) Technology
Although challenging, mastering 0BB technology could significantly reduce costs, enhance efficiency, and improve quality in photovoltaic cells, thus giving companies a technological edge. The enthusiasm for 0BB technology is high among various companies.
JinkoSolar: JinkoSolar has made the latest progress in 0BB technology, having completed development and pilot testing, and has begun applying it on a small-scale production line. The company expects to save approximately 10% of silver paste using 0BB technology. Currently, silver paste consumption is over 90 milligrams, but it is anticipated to drop to 80 milligrams in the future. The company projects that by the end of 2024, the efficiency of regular production line cells could reach over 26.5%, with the best production lines achieving 26.6-26.7%.
Canadian Solar: After more than a year of dedicated research, Canadian Solar has compared the pros and cons of various 0BB technology solutions and has identified the most suitable approach for them. The company believes that as photovoltaic technology continues to evolve and market demand changes, 0BB technology is likely to become mainstream in the photovoltaic industry.
Risen Energy: In 2023, Risen Energy utilized its proprietary 0BB cell technology, 210 ultra-thin wafer technology, pure silver usage of less than 7mg/W, and stress-free cell interconnection technology to establish a seamless production process from heterojunction silicon wafers to cells and modules. This achievement made it the first company in the industry to achieve large-scale production of heterojunction cells and modules.
Aiko Solar: Combining 0BB technology with the high conversion efficiency of ABC, Aiko Solar expects to increase the power of its ABC series products by 5W.
In summary, the application and development of 0BB technology in the market are advancing rapidly. Many companies are investing in research and trial production, and large-scale production is expected to be realized in the coming years. This will significantly reduce the cost of photovoltaic modules, improve power generation efficiency, and further drive the development of the photovoltaic industry.
Since 2008, Maysun Solar has been dedicated to producing high-quality photovoltaic modules that contribute to combating climate change. Our advanced technology in IBC, HJT, TOPCon, and balcony solar panels ensures exceptional performance and reliability, capable of withstanding harsh weather conditions for long-term operation. We have established offices and warehouses in multiple countries and built lasting partnerships with top installers to provide comprehensive support. For the latest quotes or any inquiries related to photovoltaics, feel free to reach out to us—we’re here to help!
Reference:
0BB (Busbar-Free) Aids in the Cost Reduction Process of Photovoltaics_Technology_Equipment_Solutions. (n.d.). Copyright © 2017 Sohu.com Inc. All Rights Reserved. https://www.sohu.com/a/668618791_121123896
What is 0BB that Everyone in the Photovoltaic Industry is Talking About?_Technology_Cells_Number. (n.d.). Copyright © 2017 Sohu.com Inc. All Rights Reserved. https://www.sohu.com/a/778403289_157504
Photovoltaic Companies Compete to Implement 0BB Technology: Has it Become the Best Solution for Cost Reduction and Efficiency Improvement in the Industry? _ Eastmoney. (n.d.). https://finance.eastmoney.com/a/202405083070289684.html
Xiao Hu. (n.d.). Zhonglai 0BB – Busbar-Free Cell Technology. Weixin Official Accounts Platform. https://mp.weixin.qq.com/s/j_HRtUbtvzUE-akSn0wf4w
You may also like:
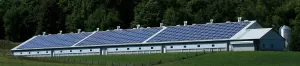
Empowering Factories with Solar Energy A Strategic Tool for Controlling Production Electricity Costs
Commercial and industrial solar is becoming a key solution for factories to reduce electricity costs and hedge against price fluctuations. This article systematically analyzes its deployment models, cost advantages, and sustainable value pathways.
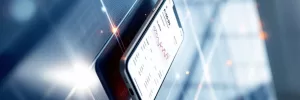
How Businesses Can Offset Carbon Taxes with Solar Power
This article analyzes the latest carbon tax policies and photovoltaic deduction strategies, helping European businesses legally reduce taxes, increase profits through solar investment, and achieve a win-win situation for both economy and environment.
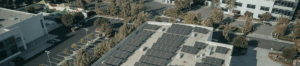
Forecast and Response: Seizing the Next Decade’s Growth Dividend in Europe’s Commercial and Industrial Photovoltaics Market
Maysun Solar analyzes the growth trends of commercial and industrial photovoltaics in Europe over the next ten years, from policies and ESG to technological innovation, helping companies seize the initiative in the energy transition.
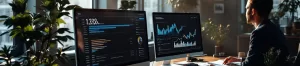
How to Calculate Solar System ROI and Optimize Long-Term Returns?
Solar power is becoming a key solution for businesses to reduce costs and improve efficiency. Accurately calculating ROI and optimizing long-term returns are essential to maximizing investment value.
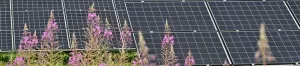
Will Agrivoltaics Affect Crop Growth?
Agrivoltaics combines solar energy and agriculture to reduce up to 700 tons of CO₂ per MW, improve water use, and boost crop growth for sustainable farming.
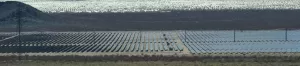
6.5 Billion Loss Hits Photovoltaics: Reshaping or Elimination?
In 2025, the photovoltaic market may see a turnaround as some companies take early action. A €6.5 billion loss is driving businesses to explore new growth areas like energy storage and hydrogen. Which giants will break through? Industry transformation is accelerating!