Table of Contents
Introduction
With the global increase in energy demand and growing awareness of environmental protection, solar energy has gained significant attention as a clean and renewable energy source. Solar panels are the core components of solar power systems, converting sunlight into electricity to provide sustainable power. This article will provide a detailed introduction to the key components and functions of solar panels, helping readers better understand their composition and characteristics.
What are Solar Panels?
Solar panels are devices that convert solar energy into electricity. They consist of multiple solar cells, which use the photovoltaic effect to convert solar energy into electrical energy. Solar panels are among the most critical parts of a solar power generation system. The typical structure of these modules includes (from top to bottom): glass—EVA film—solar cells—EVA film—backsheet or glass, secured with an aluminum alloy frame.
In addition, auxiliary materials include PV glass, encapsulation film, solder strips, backsheets, sealing silicone, AB junction box sealing gel, junction boxes, and frames.
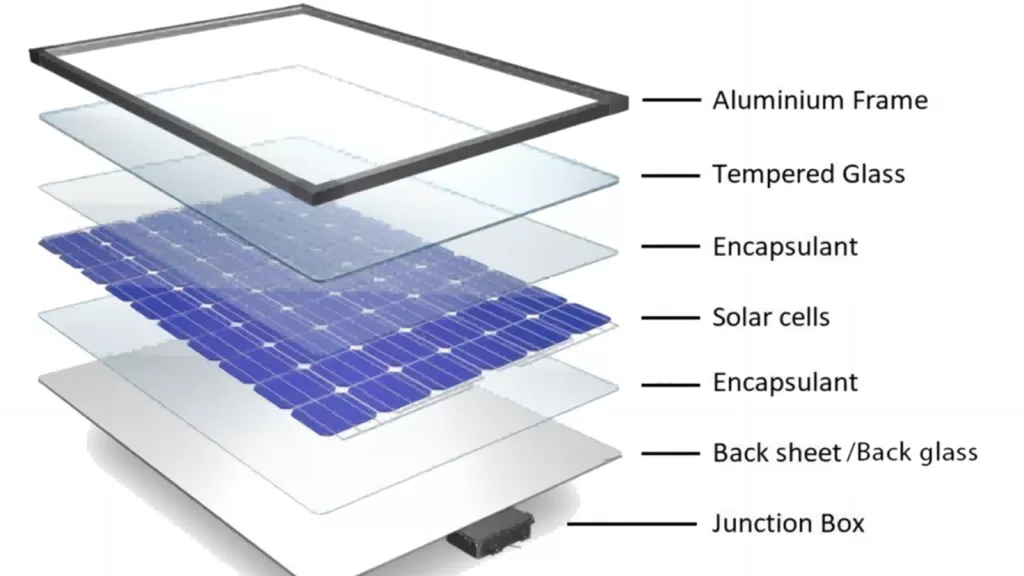
How Solar Panels Work
Solar panels collect clean, renewable energy from sunlight and convert it into electricity, which is then used to power electrical loads. Solar panels are made up of multiple individual solar cells, each composed of layers of silicon, phosphorus (providing negative charge), and boron (providing positive charge). Solar panels absorb photons (particles of light), generating an electric current. When photons strike the surface of the solar panel, they transfer their energy to electrons, causing them to break free from their atomic orbits and enter the electric field created within the solar cell. These freed electrons are then pulled into a directional current, forming what is known as the photovoltaic effect.
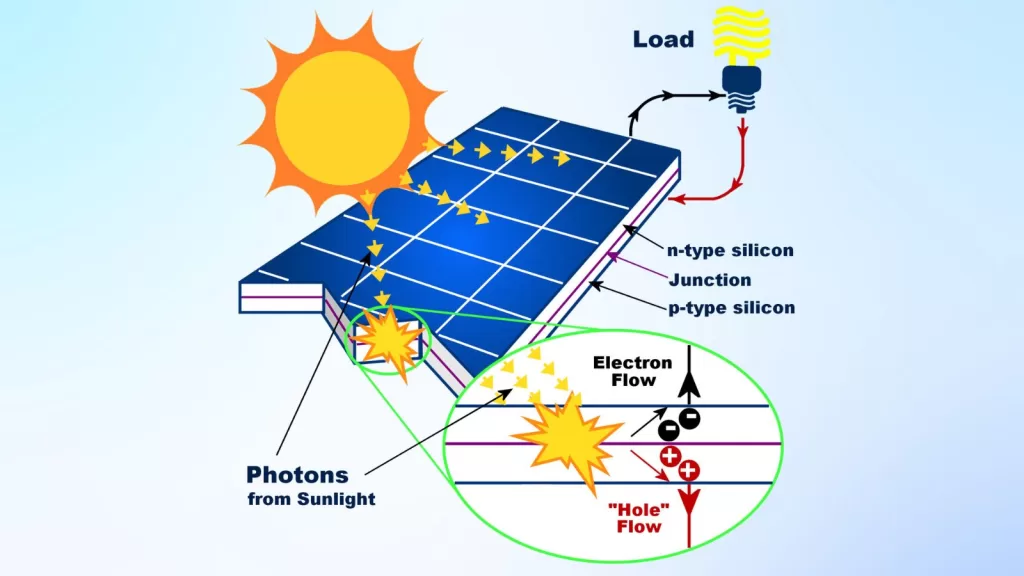
Main Components of Solar Panels
1. Solar Cells
Solar cells are one of the core components of solar panels, responsible for converting sunlight into electrical energy. They achieve this through the photovoltaic effect, where photons of sunlight hitting the surface of the solar cell excite electrons, generating an electric current that drives the flow of electrons through circuits.
(1) Types of Solar Cells
Solar cells are primarily categorized into three types based on their materials and manufacturing processes: monocrystalline silicon solar cells, polycrystalline silicon solar cells, and thin-film solar cells. Monocrystalline silicon cells are widely used due to their high crystallinity and good electron mobility. Polycrystalline silicon cells, on the other hand, are favored for their lower costs and simplified production processes. Thin-film solar cells utilize various materials such as amorphous silicon, copper indium gallium selenide (CIGS), among others, offering advantages such as lightweight, flexibility, and cost-effectiveness, making them suitable for specific applications.
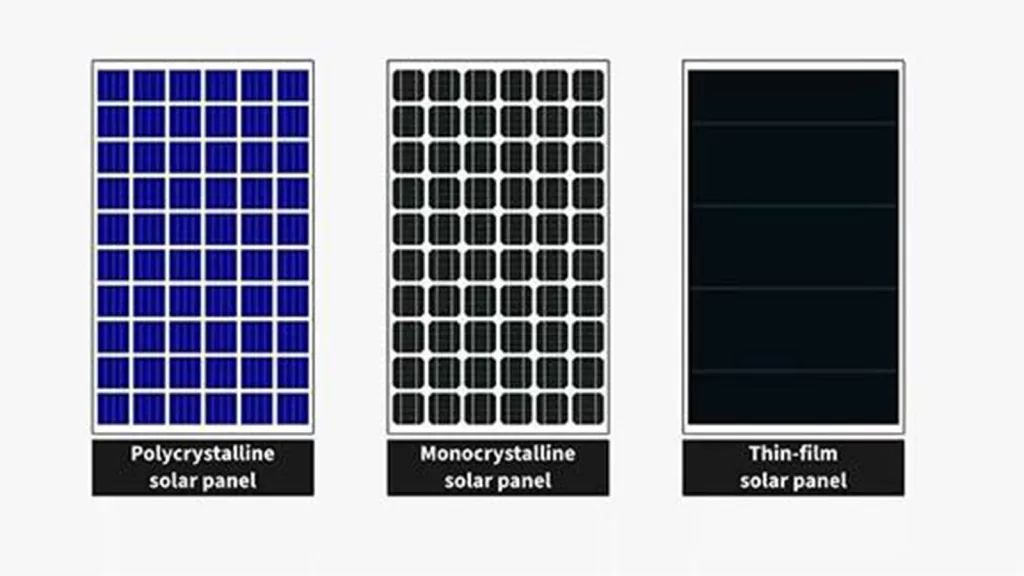
(2) Mainstream Solar Cell Technologies and Current Status
Solar cells are the core components of photovoltaic electricity generation, and their technological routes and process levels directly impact the efficiency and lifespan of photovoltaic modules. Based on doping elements and manufacturing processes, the mainstream types of solar cells currently developed and produced in the market can be broadly categorized into four types: PERC , TOPCon, HJT, and IBC.
- PERC
PERC cells (Passivated Emitter and Rear Cell) use passivated emitter and rear cell technology, with a P-type silicon wafer as the substrate for the cell’s emitter. This technology, pioneered by Australian scientist Martin Green in 1983, enhances conversion efficiency by adding a passivation layer on the rear side of the cell. By maximizing the potential gradient across the P-N junction, PERC cells stabilize electron flow, reduce electron recombination, and achieve higher efficiency levels compared to standard cell structures. - IBC
IBC cells (Interdigitated Back Contact)feature no metal grid lines on the front side. The emitter and rear field are integrated in a cross-grid pattern on the back of the cell, avoiding shading from metal grid lines. Combined with pyramid structures and anti-reflection coatings on both front and back surfaces, this unique design maximizes light utilization and significantly improves the photovoltaic conversion efficiency of IBC solar cells. - TOPCon
TOPCon (Tunnel Oxide Passivated Contact) cells employ a passivated contact structure where an ultra-thin layer of silicon dioxide is prepared on the back of the cell, followed by a layer of doped silicon. Together, these form a passivated contact structure known as TOPCon technology. The ultra-thin oxide layer allows minority carriers to tunnel into the polycrystalline silicon layer while blocking the recombination of majority carriers, enhancing lateral electron transport and collection by metal contacts. This greatly reduces recombination rates and thereby improves cell conversion efficiency. - HJT
HJT cells (Heterojunction with Intrinsic Thin-layer) are also known as heterojunction cells. Developed initially by Sanyo Electric (now Panasonic) in 1990 and trademarked as HIT, subsequent companies entering the heterojunction field adopted different designations such as HJT, SHJ, and HDT to avoid patent disputes. Unlike PERC and TOPCon cells, which use doping of the same material (crystalline silicon), HJT cells utilize doping of two different materials (crystalline silicon and amorphous silicon). This forms a PN junction between the silicon wafer and the amorphous silicon layer, reducing carrier recombination at the PN junction and thereby improving the conversion efficiency of the solar cell.
These technologies represent significant advancements in solar cell efficiency and are pivotal in the ongoing development of high-performance photovoltaic modules.
2. Front Encapsulation Material – Solar Panel Glass
Solar panels are crucial devices that convert solar energy into electricity, and their structure and material selection directly impact their efficiency and lifespan. In solar panels, the front encapsulation material is typically glass, used primarily to protect the internal solar cells while enhancing the overall performance of the panel.
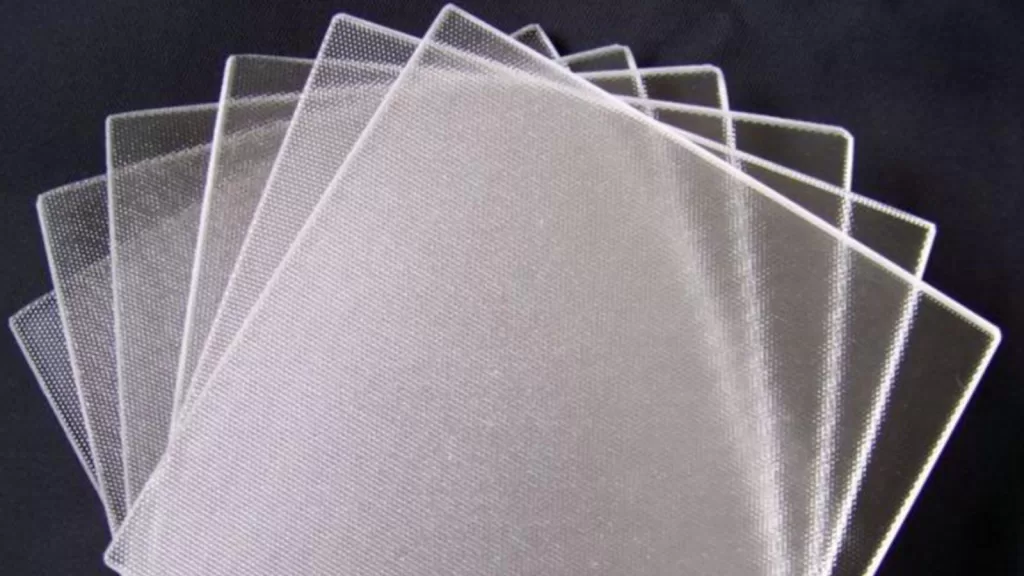
Types of Solar Panel Glass
Ultra-clear Glass: Also known as low-iron glass, it has extremely high light transmittance (up to 91%-93%) and is widely used in high-efficiency solar panels. Ultra-clear glass has very low iron content, reducing light absorption and improving light transmittance.
Tempered Glass: Glass strengthened by physical or chemical methods, it has high strength and impact resistance. Even if shattered, it breaks into small granular pieces, reducing damage to the solar cells. Tempered glass is commonly used in solar panels that require high mechanical strength.
Semi-tempered Glass: Semi-tempered glass has stress levels between ordinary flat glass and fully tempered glass, ranging from 24MPa to 52MPa. Despite lower impact resistance, it has high flatness and no internal stress, making it suitable for lamination processing in solar panel production, thus improving yield and quality.
Coated Glass: Glass with a special thin film coating on the surface, which reduces reflection, increases light transmittance, and provides anti-soiling and waterproof functions. It is suitable for solar panels in special environmental conditions.
Functions and Roles of Solar Panel Glass
As a critical component covering the solar cells, solar panel glass performs multiple crucial functions that directly impact the performance and durability of the entire solar panel module.
High Light Transmittance: High-quality PV glass typically has light transmittance above 90%, ensuring more sunlight reaches the solar cells through the glass, thereby enhancing photovoltaic conversion efficiency.
Weather Resistance: PV glass needs to operate long-term under various environmental conditions, requiring high weather resistance to maintain stable performance in harsh environments such as high temperatures, low temperatures, humidity, and UV exposure, without aging, discoloration, or failure.
Mechanical Strength: Using tempered glass with high strength and impact resistance can withstand external pressures such as wind load, snow load, and hail, ensuring long-term safety and usability.
Low Iron Content: Low-iron glass (ultra-clear glass) has very low iron content, reducing light absorption and improving light transmittance, significantly enhancing photovoltaic conversion efficiency.
Anti-reflective Coating: Adding anti-reflective coatings reduces light reflection losses, further increasing light transmittance so that more light enters the solar cells, thereby improving overall photovoltaic conversion efficiency.
3. Solar Panel Encapsulation Film
Encapsulation film is a crucial material in photovoltaic (PV) module packaging and is essential for the module’s lifespan. It seals and bonds to protect the internal cells of the module. Encapsulation films include EVA, POE, and co-extruded EPE.
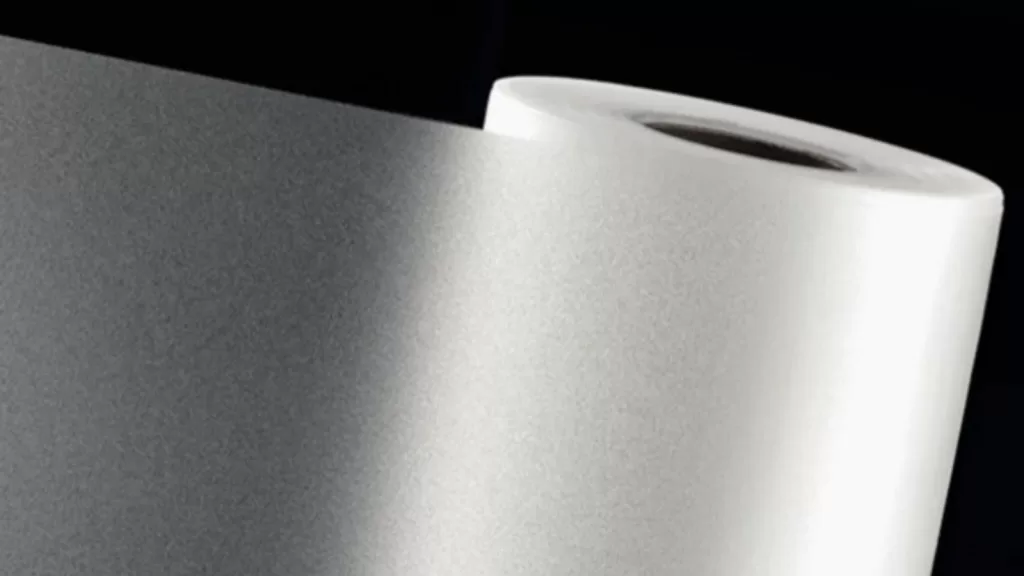
EVA: EVA film is one of the most widely used encapsulation materials, especially suitable for encapsulating mono-glass P-type PERC modules. This material is cost-effective, offers good processability, and has a fast cross-linking speed, effectively protecting cells from environmental impacts. Depending on specific needs, different types of EVA can be chosen, such as high transparency EVA for the front, high cutoff EVA for the back, or white EVA made with titanium dioxide.
POE: POE film is primarily used for double-glass and N-type PV module encapsulation. Compared to EVA, POE exhibits superior properties including low water permeability, hydrolysis resistance, aging resistance, and excellent PID (Potential Induced Degradation) resistance. However, its smooth surface makes it prone to displacement and increases processing difficulty, resulting in higher costs.
Co-extruded EPE: Co-extruded EPE film combines the good processability of EVA with the excellent PID resistance and water vapor resistance of POE. This material is commonly used in N-type Topcon cell modules and double-glass modules, striking a balance between performance and cost-effectiveness.
Key Characteristics of Solar Panel Encapsulation Films
In solar panels, encapsulation films must possess several key characteristics to ensure their effectiveness and reliability in the photovoltaic conversion process:
High Transparency: The transparency of encapsulation films should be as high as possible to allow maximum sunlight penetration, thereby improving photovoltaic conversion efficiency. Typically, the transparency requirement is above 95%.
Low Optical Loss: Encapsulation films should minimize optical losses to reduce light absorption and scattering within the film. Optical losses primarily include absorption and scattering losses.
Excellent Adhesion: Encapsulation films should exhibit strong adhesion to materials such as glass, cells, and back sheets, ensuring the module’s robustness and reliability. The bonding strength between the encapsulation film and cells should be sufficient to withstand mechanical stress during module operation.
Good Mechanical Strength: Encapsulation films should have adequate mechanical strength to withstand mechanical loads under harsh environmental conditions such as wind, snow, and hail.
Excellent Electrical Insulation: Encapsulation films should effectively prevent leakage and electrical accidents, ensuring the safety and reliability of the PV system. The breakdown voltage and volume resistivity of the encapsulation film should meet relevant standard requirements.
4. Solar Panel Backsheet
In the backside encapsulation of solar photovoltaic (PV) modules, the materials primarily include the backsheets and back glass, playing a crucial role in protecting and optimizing the module’s performance.
Backsheets:
Located on the rear side of solar panels, the backsheet’s main function is to shield the internal solar cells and encapsulation materials from external environmental corrosion and damage, ensuring long-term stable operation of the module. Common materials for backsheets include Fiberglass Reinforced Plastic (FRP) and Polyester Film Backsheets. FRP backsheets offer high strength and weather resistance, suitable for various environmental conditions. Polyester film backsheets are lightweight and possess good flexibility and mechanical properties.
Backsheets typically consist of a three-layer structure, comprising an outer layer, a middle layer (commonly PET substrate), and an inner layer. Various types of coated backsheets, including FPF, KPF, PPF, and PF, offer different characteristics such as fluorine coatings (F or C) and PVDF films (K) that enhance weather resistance and anti-aging properties. These layered structures and coatings effectively shield the module’s internal components from light, moisture, heat, and freezing conditions, thereby ensuring its stability and reliability across diverse environmental settings.
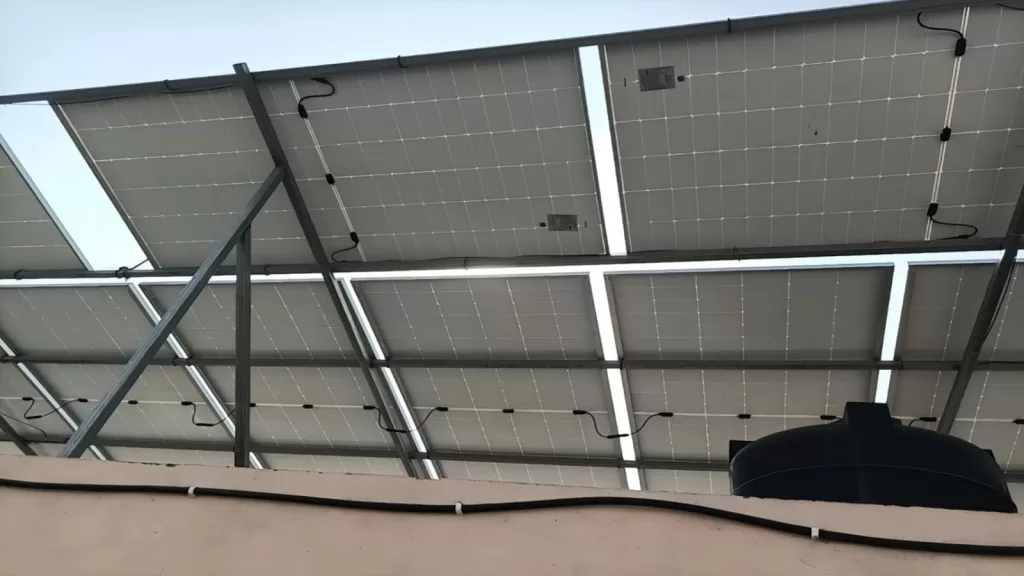
Back Glass:
Back glass is the glass material covering the backsheet in solar panels. Its primary role is to protect the rear structure and maximize light transmission to enhance the module’s photovoltaic conversion efficiency. Back glass also boasts excellent abrasion resistance, weather resistance, and corrosion resistance, making it suitable for long-term use in various environmental conditions.
Back glass typically uses semi-tempered low-iron ultra-clear photovoltaic glass. It comes in different thicknesses (such as 2.0mm and 1.6mm) and designs with or without grids to meet the requirements of different applications. Its characteristics include extremely low water vapor transmission rates, which prevent moisture-induced backsheet delamination issues. Additionally, it has high insulation properties, supporting higher system voltage requirements.
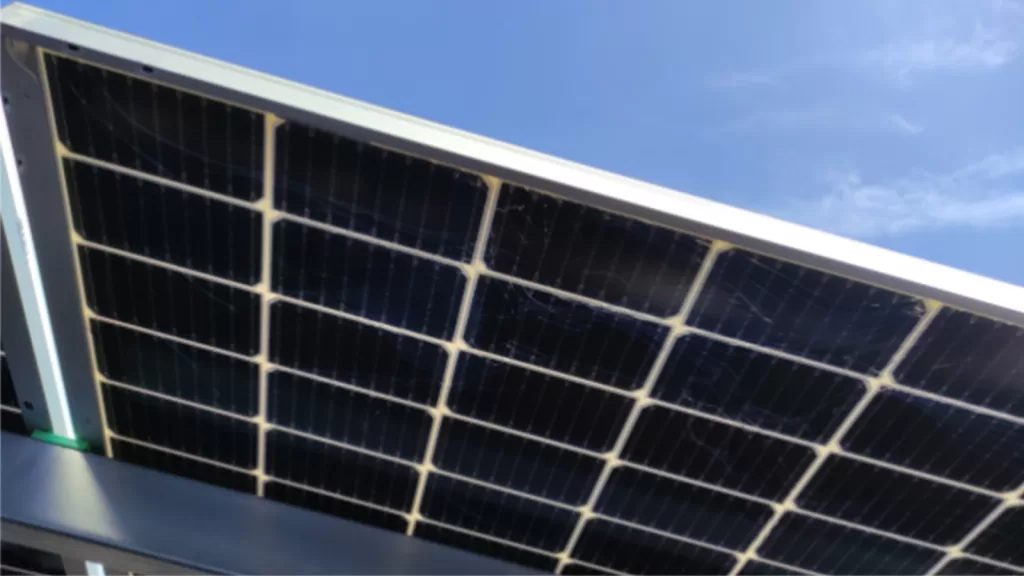
5. Solar Panel Frame:
The solar panel frame is an essential accessory of the module, primarily used to protect the edges of the solar panel glass, enhance module sealing performance, and improve mechanical strength, significantly impacting module lifespan. As a crucial component in the photovoltaic module, aluminum alloy frames have dominated the market due to their high strength, robustness, good conductivity, corrosion resistance, oxidation resistance, strong tensile strength, convenience in transportation and installation, and ease of recyclability. These excellent properties have enabled aluminum alloy frames to maintain a market penetration rate of over 95%, evolving alongside the photovoltaic industry over the years.
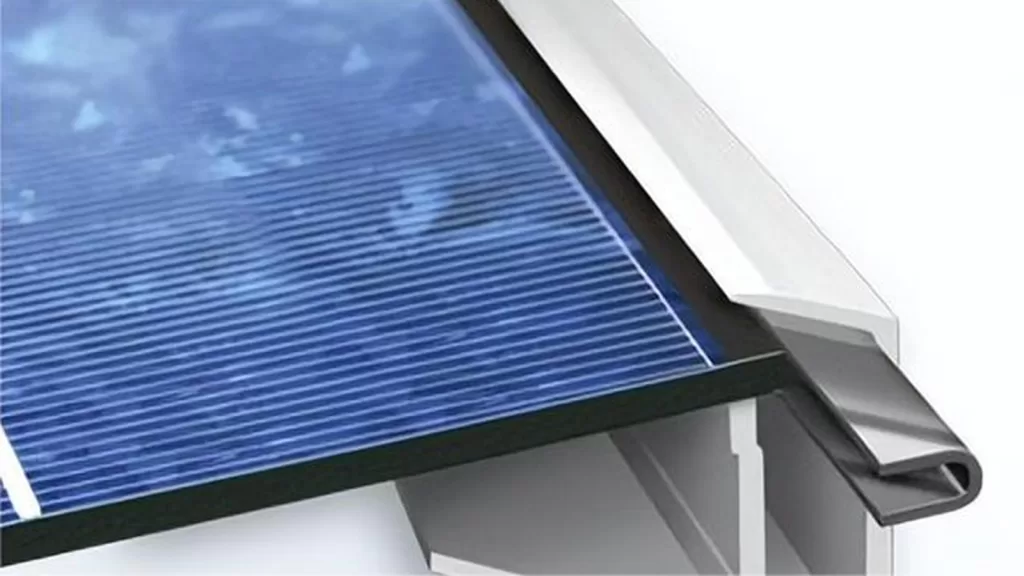
The solar panel frame is a high-value component accessory in the cost structure of photovoltaic modules, where cell costs constitute about 55%. With current standard sizes and weights of aluminum frames, solar panel frame account for approximately 13% of the total cost, higher than other accessories such as EVA, glass, backsheet, and ribbons. It is the highest-cost accessory. Besides traditional aluminum alloy frames, there are also low-cost aluminum-magnesium alloy frames and composite material frames in the market. However, due to limitations in appearance and corrosion resistance, these materials have not become mainstream choices.
6. Junction Box:
The junction box is a connector located between the solar photovoltaic cell array forming the solar panel and the solar charging control device. Its primary function is to connect the electricity generated by the solar photovoltaic cells to external circuits. The junction box is adhered to the module’s backsheet with silicone. The outgoing wires inside the module are connected together through the internal wiring of the junction box, which then connects the internal wiring to the external cables, ensuring the module’s connection to external cables.
The junction box of the photovoltaic module is a critical electrical connection component. Its main structure includes a housing with a printed circuit board inside. The printed circuit board has N busbar connection terminals and two cable connection terminals. Each busbar connection terminal is connected in series with the strings of solar photovoltaic cells via busbars, and adjacent busbar connection terminals are connected by diodes. Electronic switches are serially connected between the busbar connection terminals and the cable connection terminals, controlled by received control signals to turn them on or off. The Nth busbar connection terminal is connected to the second cable connection terminal. The two cable connection terminals are connected to the outside world via cables, and a bypass capacitor is also placed between the two cable connection terminals.
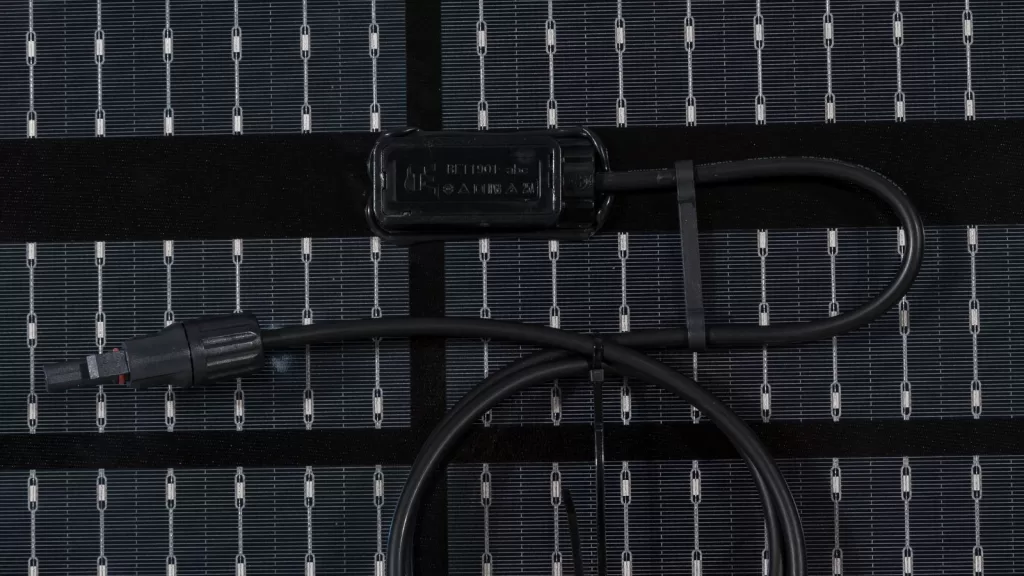
Conclusion
In summary, the composition of a solar photovoltaic module includes key components such as photovoltaic cells, backsheet, glass, encapsulation materials, frame, and junction box. Each component plays an indispensable role in overall performance and durability. Photovoltaic cells are the core, responsible for converting solar energy into electricity; the backsheet and glass provide protection and transparency; encapsulation materials ensure sealing and durability of each part; while the frame and junction box are responsible for module fixation, installation, and current conduction. The synergistic effect of these components enables solar photovoltaic modules to operate efficiently and stably, meeting the diverse needs of various applications.
Since 2008, Maysun Solar’s goal has been to produce the best solar panels. Explore our extensive range of TOPCon, IBC, HJT solar panels, available in silver, full black, black frame, and glass-glass styles. Our beautifully designed and highly efficient panels not only stand out but also enhance the aesthetics of any building. With long-standing offices and warehouses and established relationships with top installers in many countries, Maysun Solar is a reliable choice. If you have any questions about solar panels or would like the latest quotes, please feel free to contact us. We’re happy to help.
Reference:
Solar Panels: A Brief Analysis of Process Route Development Status – Efficiency – Composite – Technology. (n.d.-c). Copyright © 2017 Sohu.com Inc. All Rights Reserved. Retrieved from https://www.sohu.com/a/635276105_121123896
What Is A Solar Panel? How does a solar panel work? (n.d.). https://www.mrsolar.com/what-is-a-solar-panel/
EcoProgetti. (2021, July 9). The structure of a photovoltaic module. Ecoprogetti | Specialist in Photovoltaic Production Process. https://ecoprogetti.com/the-structure-of-photovoltaic-module/
What is the role of the middle junction box of the photovoltaic module, photovoltaic panel junction box 4 terminals how to wire – cocoon cloud voltaic. (n.d.-b). https://www.pojianyunfu.com/news/1127.html
Photovoltaic frame is one of the important auxiliary materials of the module, mainly used to protect the edge of the photovoltaic glass, strengthen the module sealing. . . (n.d.-c). https://mguangfu.bjx.com.cn/mnews/20230831/1329267.shtml
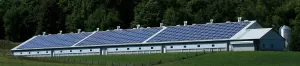
Empowering Factories with Solar Energy A Strategic Tool for Controlling Production Electricity Costs
Commercial and industrial solar is becoming a key solution for factories to reduce electricity costs and hedge against price fluctuations. This article systematically analyzes its deployment models, cost advantages, and sustainable value pathways.
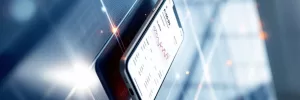
How Businesses Can Offset Carbon Taxes with Solar Power
This article analyzes the latest carbon tax policies and photovoltaic deduction strategies, helping European businesses legally reduce taxes, increase profits through solar investment, and achieve a win-win situation for both economy and environment.
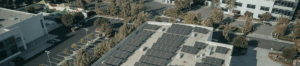
Forecast and Response: Seizing the Next Decade’s Growth Dividend in Europe’s Commercial and Industrial Photovoltaics Market
Maysun Solar analyzes the growth trends of commercial and industrial photovoltaics in Europe over the next ten years, from policies and ESG to technological innovation, helping companies seize the initiative in the energy transition.
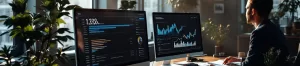
How to Calculate Solar System ROI and Optimize Long-Term Returns?
Solar power is becoming a key solution for businesses to reduce costs and improve efficiency. Accurately calculating ROI and optimizing long-term returns are essential to maximizing investment value.
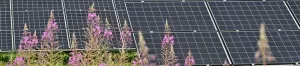
Will Agrivoltaics Affect Crop Growth?
Agrivoltaics combines solar energy and agriculture to reduce up to 700 tons of CO₂ per MW, improve water use, and boost crop growth for sustainable farming.
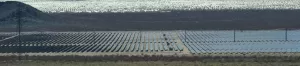
6.5 Billion Loss Hits Photovoltaics: Reshaping or Elimination?
In 2025, the photovoltaic market may see a turnaround as some companies take early action. A €6.5 billion loss is driving businesses to explore new growth areas like energy storage and hydrogen. Which giants will break through? Industry transformation is accelerating!