Intro:
The quality of solar glass, backsheets and encapsulation materials, which are key components of Solar cell lamination, affects the reliability of Solar modules. Any low-quality component accelerates the aging of the solar module. Substandard Solar panel Backsheets can lead to reduced performance, increased maintenance costs, and further costs associated with inspection and laboratory evaluation or replacement. Therefore, ensuring that your solar panels are equipped with high-quality backsheets is critical to the long-term sustainability of your photovoltaic modules.
Table of Contents
What are Solar panel Backsheets?
The solar panel backsheet serves as the outermost layer of a photovoltaic (photovoltaic) module, serving multiple crucial roles. It is primarily designed to shield the photovoltaic cells and internal electrical components while also providing electrical insulation.
Additionally, the backsheet acts as a robust weatherproof barrier, safeguarding the module against environmental elements such as rain, moisture, and other adverse conditions.、
Backsheets are usually available in all-white, all-black, white on the outside and black on the inside, and transparent colors (clear backsheets). The white color is conducive to the light reflection of the gap between the cells to the front surface, part of the light will be reflected back to the solar cell, increasing the utilization of light energy by the solar cell, which is conducive to the improvement of the photoelectric conversion efficiency, black backsheets are more popular with customers in Europe because they look better on the roof.
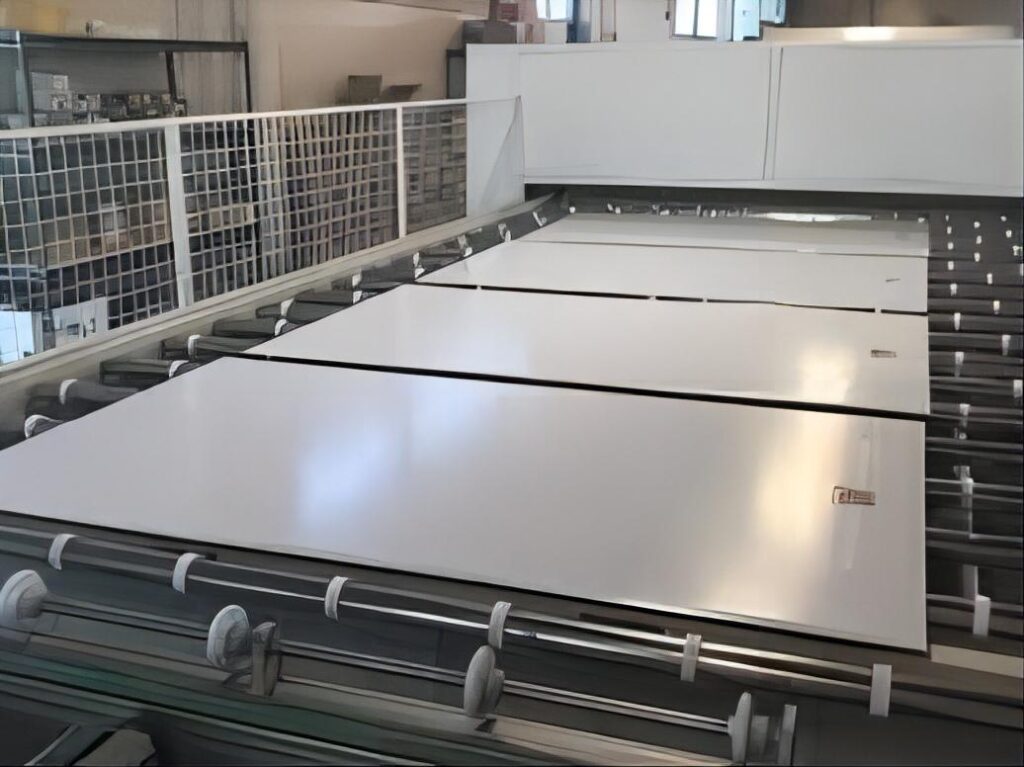
What Certifications Are Required for Solar Panel Backsheets?
Solar panel backsheets typically need to undergo TUV certification, an internationally recognized testing and certification body. The TUV certification primarily involves partial discharge testing to ensure the quality and performance of the backsheet meets specific standards and requirements.Solar panel backsheets typically need to undergo TUV certification, an internationally recognized testing and certification body. The TUV certification primarily involves partial discharge testing to ensure the quality and performance of the backsheet meets specific standards and requirements. As the photovoltaic industry continually seeks higher power generation efficiency, some high-performance solar backsheets also have a higher light reflectance to enhance the photovoltaic conversion efficiency of solar modules.
What’s The Structure Of the Solar Panel Backsheet?
Initially, solar backsheets had a three-layer structure (PVDF/PET/PVDF). The outer PVDF layer offers excellent environmental corrosion resistance, the middle PET layer provides insulation, and the inner PVDF layer, combined with EVA, ensures good adhesion. To reduce costs and consider environmental factors, fluorine-free backsheet structures, such as the APE structure, were introduced.
A typical backsheet is composed of three core layers:
Outer Protective Layer (Weathering Layer): For optimal weather resistance, the outer layer material usually contains fluorine. PVF and PVDF are well-known polymers with high weather resistance. Some manufacturers also use THV, ETFE, ECTFE, and coated PTFE.
Middle Layer: This layer provides support and must withstand temperature fluctuations. It should have stable mechanical properties, excellent electrical insulation, and low gas and vapor permeability. Modified PET material is commonly used.
Lamination Adhesive Layer: Unmodified fluorine films and PET have poor adhesion to EVA, so modified fluorine materials or adhesives like EVA, PE, or PA films are used.
What Are the Different Types of Solar Panel Backsheets?
Backsheets fall into three primary categories: bifluoropolymers, monofluoropolymers, and non-fluoropolymers, with multiple structural variations within each category.
1.Double-sided fluorine film composite backsheet
A. TPT Backsheet (PVF/PET/PVF)
The TPT backsheet, using a composite process, is the most common type of double-sided fluoropolymer backsheet available in the market. It combines DuPont’s Tedlar brand PVF fluorine film from the United States with an intermediate layer of PET base film, bonded together with adhesive. The inner fluorine material shields the PET from UV corrosion, and with special treatment and encapsulation of the adhesive film, it enhances bonding. The outer fluorine material provides protection for the back of the solar module against moisture, heat, and UV erosion.
B.KPK Backsheet (PVDF/PET/PVDF)
Compared to TPT, the KPK backsheet differs in that it uses PVDF film for both the inner and outer fluorine layers. This type of backsheet is known for its high mechanical strength, excellent irradiation resistance, good chemical stability, and resistance to corrosion by acids, alkalis, strong oxidizing agents, and halogens at room temperature. Originally, this backsheet was referred to as the KPK backsheet, made from Arkema France’s Kynar brand PVDF fluorine film.
C.KPF Backsheet (PVDF/PET/Fluorine Skin Film)
The KPF backsheet employs a composite process, laminating PVDF fluorine film to one side of the PET base film using adhesive. On the other side, a fluorine resin mixed with titanium dioxide is evenly coated onto the PET base film through a cast filming process. After a high-temperature maturation process, this coating forms a self-adhesive fluorine skin film, which is different from traditional fluorine coatings that tend to peel off easily. The fluorine skin film meets the high-performance requirements of foreign fluorine film products, including UV resistance and water resistance, while significantly reducing costs.esistance, while the price is significantly reduced.
2.Single-side fluorine film composite backsheet
A.TPE Type Backsheet (PVF/PET/PE)
The TPE type backsheet (PVF/PET/PE) primarily employs PE (polyolefin film) in place of the inner fluorine film. Due to the single-sided fluorine protection, it does not offer the same level of protection as the TPT structure, making it less capable of withstanding long-term UV aging tests. However, it presents a cost-effective alternative with lower expenses compared to the TPT structure.
B.KPE Type Backsheet (PVDF/PET/PE)
The KPE type backsheet (PVDF/PET/PE) largely relies on PE (polyolefin film) as a substitute for the inner fluorine film. With fluorine protection on one side, its protective performance is not as robust as that of the KPK-type backsheet, and it may struggle to endure prolonged UV aging tests. Nevertheless, it provides a more budget-friendly solution when compared to the FPF structure.
3.Non-fluoropolymers:
This category involves two layers of PT and a primer or EVA layer, making it the most cost-effective choice. While it had been less favored in the past due to potential degradation from prolonged UV exposure or hydrolysis, advances in polycool chemistry and production engineering have facilitated the development of highly UV-resistant polycool films.
Maysun Solar’s IBC solar modules employ a TPE backsheet, characterized by its high UV resistance, anti-aging properties, low water permeability, and coated with PVF (Tedlar) film. This choice underpins our commitment to a 25-year quality guarantee.
What Functions Of Solar Panel Backsheets?
1. Mechanical Stress Resistance:
The backsheet plays a critical role in fortifying the structural integrity of solar modules. It serves as a protective shield against various mechanical stresses that could potentially inflict harm. These stresses encompass forces like pressure, impacts, vibrations, and external factors such as wind, snow, falling objects, or seismic activity. Without a reliable backsheet, solar cells and electrical components become susceptible to damage from these sources.
2.Protection from Water and Dust Ingress:
One of the key functions of the backsheet is to act as a barrier against water and dust infiltration. Water and dust particles can lead to corrosion and pitting, posing a threat to photovoltaic cells. The backsheet’s role is to shield against moisture-related damage, including corrosion of electrical connections, insulation degradation, and the risk of short circuits. It also safeguards against dust accumulation on the cell surface, which can reduce system efficiency or even lead to operational disruptions.
3.Ultraviolet (UV) Radiation Shield:
Solar panel backsheets serve as a crucial defense against the potentially harmful effects of UV radiation. UV rays can cause semiconductor materials within the solar cells to degrade, diminishing their performance and efficiency. The backsheet acts as a shield, protecting the cells from UV radiation. It’s important to note that over time, all backsheets will undergo a color change due to UV exposure. While a change in color isn’t necessarily a sign of a defective backsheet, significant color changes and signs of deterioration may warrant further inspection.
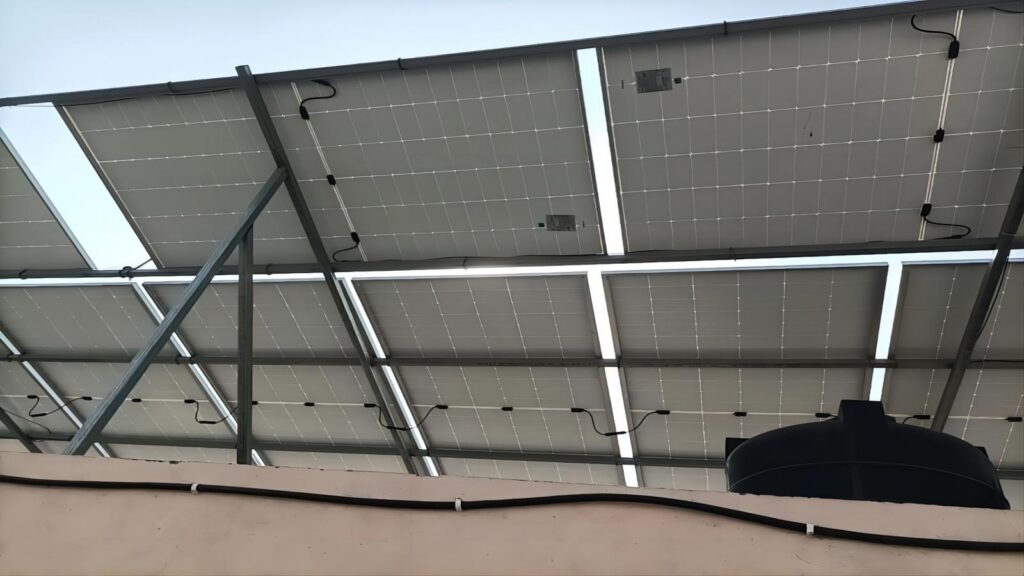
4. Temperature Stress Management:
Backsheets also serve a critical function in managing temperature-related stress in photovoltaic modules. Solar cells are subject to thermal stress when exposed to extreme heat or cold, which can impact their efficiency. Backsheets act as insulators, safeguarding the system against temperature extremes and mitigating thermal stress. Additionally, they help regulate solar heat absorption by preventing high-energy photons from reaching the photovoltaic cells, thus averting overheating that can compromise performance. As temperatures rise beyond a certain threshold, solar cell efficiency decreases, making the control of heat gain essential. Backsheets play a significant role in reducing solar heat gain and preventing cell overheating.
5.Dielectric Integrity:
A solar panel operates as an isolated electrical system, requiring immunity to external electrical interference. The backsheet serves as a protective shield, preventing electrical conductivity between the solar cell and its environment. Dielectric strength is a measure of a material’s ability to withstand electrical potential without suffering breakdown or loss of insulation. Materials with high dielectric strength can endure high voltages without experiencing dielectric failure. Maintaining the backsheet’s electrical integrity is crucial to preventing external interference with the solar cells, ensuring the system operates efficiently and without disruptions. Using the correct type of backsheet to insulate the solar cells is essential to minimize the risk of short circuits and other electrical issues
Which Backsheet is Best for your solar panels?
Solar panels come in a multitude of types, each with specific needs when it comes to their backsheet selection. In most cases, normal backsheets are sufficient to meet the requirements of PERC (Passivated Emitter Rear Cell) solar panels. However, when it comes to N-type or N-type TOPCon (Tunnel Oxide Passivated Contact) solar panels, a more specialized approach is necessary.
For N-type and N-type TOPCon solar panels, it’s crucial to opt for a backsheet with a water permeability rate of ≤0.15 grams per square meter or a completely impermeable glass backsheet. This selection should also be coupled with the appropriate use of POE (Polyolefin Elastomer) and EPE (Ethylene Propylene Elastomer) films to ensure the safe and reliable operation of these solar panels.
HJT (Heterojunction) solar panels raise the bar even higher in terms of water permeability requirements. Standard backsheets simply can’t meet the stringent demand for zero water permeability. Consequently, the only viable option is to go with a glass backsheet. Maysun has introduced HJT solar modules that feature a double-sided glass design to fulfill these exacting criteria.
It’s worth noting that a limited number of N-type TOPCon and HJT solar panels opt for PAPF (Polymer-Aluminum-Polymer Film) backsheets. However, this choice comes with the inherent risk of electrical leakage and is still awaiting comprehensive experimental data validation. As a result, its widespread adoption remains limited
Why does the Solar panel Backsheet have problems?
1.Subpar Core Material:
One of the primary reasons for backsheet failure is the use of inexpensive materials, particularly low-stability PET, in the core layer. While PET polymers offer decent electrical insulation, they are highly susceptible to moisture and sunlight, making them unsuitable for outdoor applications.
2.Cost-Cutting Measures:
Driven by cost concerns, manufacturers have been progressively reducing the thickness of the outer protective layer while the PET core remains vulnerable to moisture. The market is flooded with backsheets featuring outer films of fluoropolymer that are less than 20 microns thick, a significant reduction from the previous 40+ microns. In some instances, the outer “protective” layer can be as thin as 10 microns, rendering the backsheet highly susceptible to accelerated damage.
3.Cost-Driven Production Practices:
Certain gaps in the certification process permit manufacturers to cut corners in their production methods. This includes sourcing components of the bill of materials from various suppliers and using a range of adhesives that may not meet the most recent certification standards. Predictably, this practice can lead to backsheet failures, making it challenging to pinpoint the exact cause behind each failure.
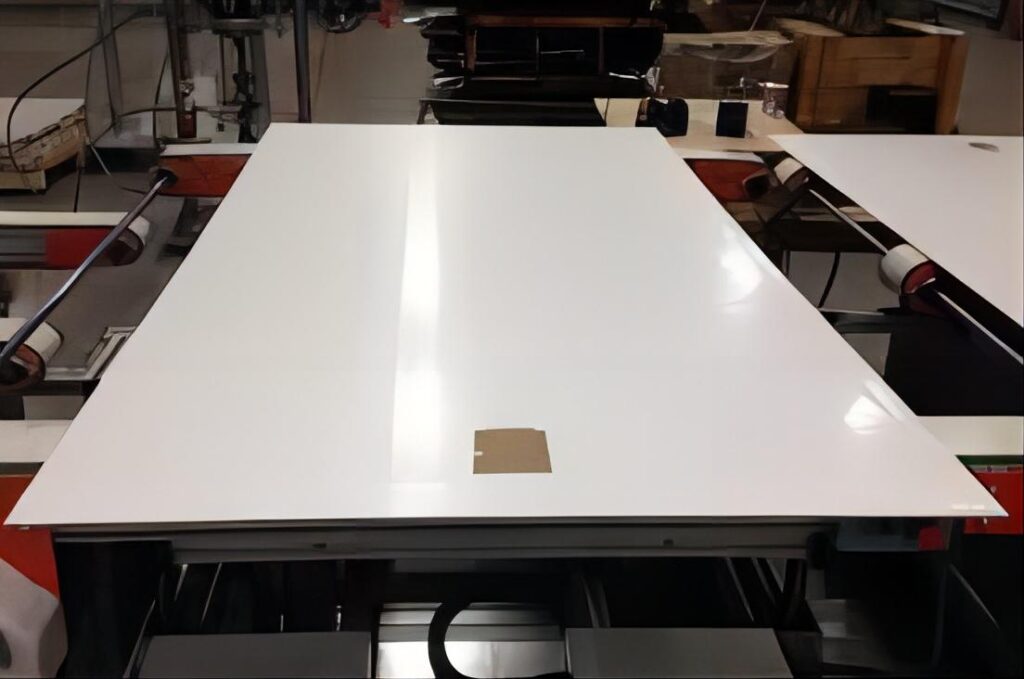
What Are The Market Trends For Backsheets?
1.By Product:
In 2016, TPT secured a market share of over 12% in the Solar market. In the current industrial landscape, this technology presents an economically viable alternative to TPT configurations. These products have gained significant traction thanks to the availability of cost-effective and efficient auxiliary backsheet technologies. Rapid technological advancements aimed at enhancing operational flexibility and efficiency are anticipated to drive the demand for these products.
2.By Thickness:
Backsheets with a thickness of less than 100 microns are poised for robust growth, owing to reduced product costs and their extensive deployment in small- and large-scale solar applications. The utility-based implementation and the ongoing adoption of photovoltaic technology to establish sustainable energy portfolios across various sectors will expand the Solar panel Backsheet market for thicknesses exceeding 500 microns.
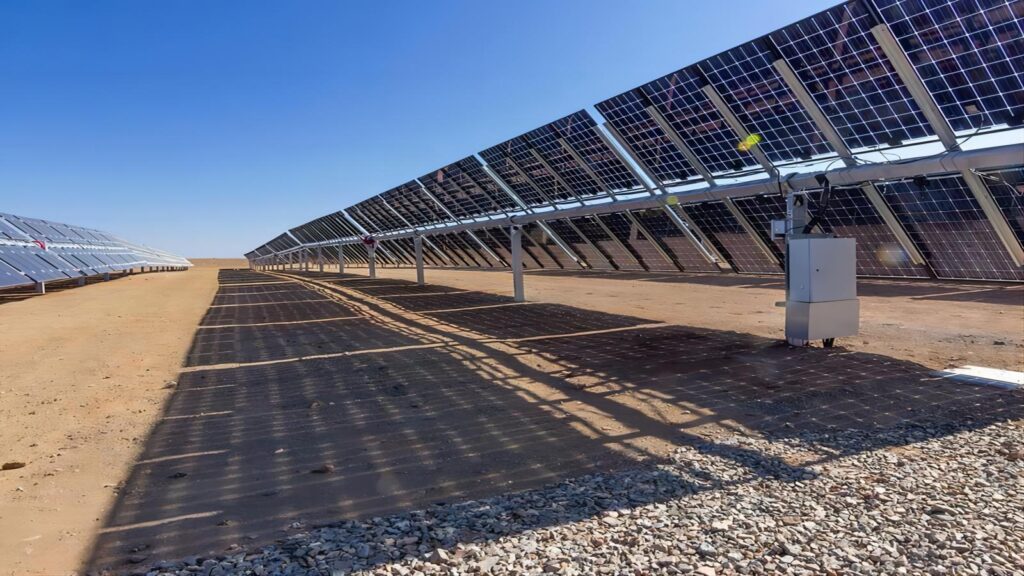
3.By Material:
Fluoropolymers contribute to over 50% of the global Solar panel Backsheet market, primarily due to their early adoption and extended lifespan. These products offer superior efficiency and insulation properties compared to non-fluorinated alternatives. However, recent years have witnessed a shift towards cleaner auxiliary backsheet technologies as consumers prioritize fluorine-free options.
4.By Technology:
The crystalline Solar panel Backsheet market is projected to grow by more than 4% by 2024. The increased prevalence of crystalline cells and their widespread deployment has heightened the demand for support and insulation materials. Improving product efficiency and the development of compact panel structures will stimulate the adoption of advanced backsheet technologies in crystalline photovoltaic modules.
Maysun Solar offers a wide selection of solar panels, including shingled, half-cut, black frame, full black frame, and silver frame. These solar panels are made with excellent quality solar backsheets to protect your solar panels from external forces. Maysun Solar has global offices and warehouses and has established strong cooperative relationships with well-known installers. Our solar panel installation process is simple and easy, ensuring continued clean energy production and maintenance. If you have any photovoltaic-related inquiries or want to know the latest module prices, please contact us.
Saurenergy (2018b) BACKSHEETS selecting the right materials for solar modules & EVA.
Solaradvisor (2021) ‘Solar Panel Backsheets: [All To Know About] | Solartechadvisor,’ Solartechadvisor, 28 November.
manager@vishakharenewables (2023) How does backsheet quality impact modern solar PV modules?
Spw (2020) How backsheet quality impacts modern solar PV modules.
What is a solar cell backsheet? What is the function of a module backsheet?_Mibet New Energy (no date). https://www.mbt-energy.cn/news/industry/2308172.html.
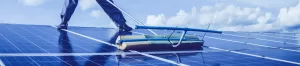
How to Effectively Clean and Intelligently Maintain Photovoltaic Systems for Optimal Performance?
Explore how scientific cleaning and intelligent maintenance can ensure the efficient operation of commercial and industrial photovoltaic systems. Practical advice covers module cleaning frequency, monitoring system configuration, and long-term strategies for energy savings and performance enhancement.
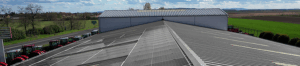
2025 European Photovoltaic Policy Map: Deployment Paths and Regional Strategies for Commercial and Industrial Photovoltaics
A comprehensive analysis of the 2025 European commercial and industrial photovoltaic policy map, focusing on deployment strategies, incentive comparisons, and zero-investment models to support businesses in achieving an efficient and green transition.
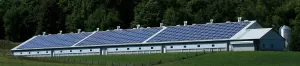
Empowering Factories with Solar Energy A Strategic Tool for Controlling Production Electricity Costs
Commercial and industrial solar is becoming a key solution for factories to reduce electricity costs and hedge against price fluctuations. This article systematically analyzes its deployment models, cost advantages, and sustainable value pathways.
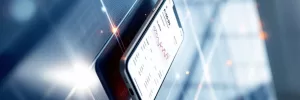
How Businesses Can Offset Carbon Taxes with Solar Power
This article analyzes the latest carbon tax policies and photovoltaic deduction strategies, helping European businesses legally reduce taxes, increase profits through solar investment, and achieve a win-win situation for both economy and environment.
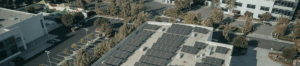
Forecast and Response: Seizing the Next Decade’s Growth Dividend in Europe’s Commercial and Industrial Photovoltaics Market
Maysun Solar analyzes the growth trends of commercial and industrial photovoltaics in Europe over the next ten years, from policies and ESG to technological innovation, helping companies seize the initiative in the energy transition.
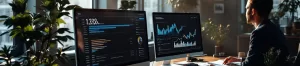
How to Calculate Solar System ROI and Optimize Long-Term Returns?
Solar power is becoming a key solution for businesses to reduce costs and improve efficiency. Accurately calculating ROI and optimizing long-term returns are essential to maximizing investment value.