Solar panels convert light into power, converting energy everywhere. However making solar panels requires complex material structures and production processes, read this article to learn more about each process!
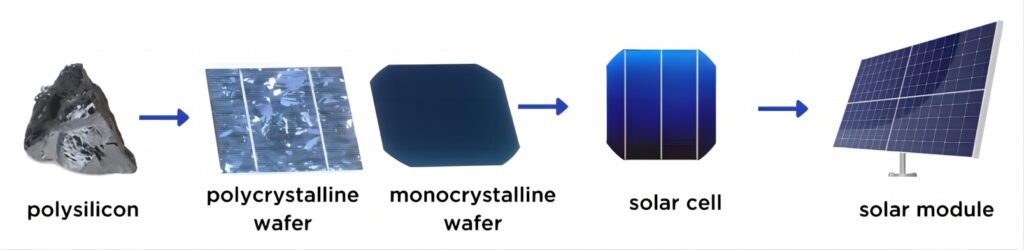
Materials and structure of solar panels
The main packaging auxiliary materials for PV modules include glass, aluminium frame, EVA, etc., which provide protection for the cells. Maysun has undergone high-standard material selection, precise processing and manufacturing, and strict performance testing. This ensures that we can use high-quality PV modules in different climate environments, providing guarantees for performance and durability.
How does a solar panel resist rain and snow with its internal structure? The usual structure from top to bottom includes: PV glass, EVA, cells, EVA, backplane/PV glass, and aluminium alloy frame and junction box. However, creating a high-quality solar panel requires more than just assembling these materials. It must undergo a series of rigorous processes and successfully pass numerous tests.
In short, a number of specialists and 20-25 machines closely work together from cell to module. The process revolves around ten major steps, which divide into several sub-steps, to produce a complete solar panel.
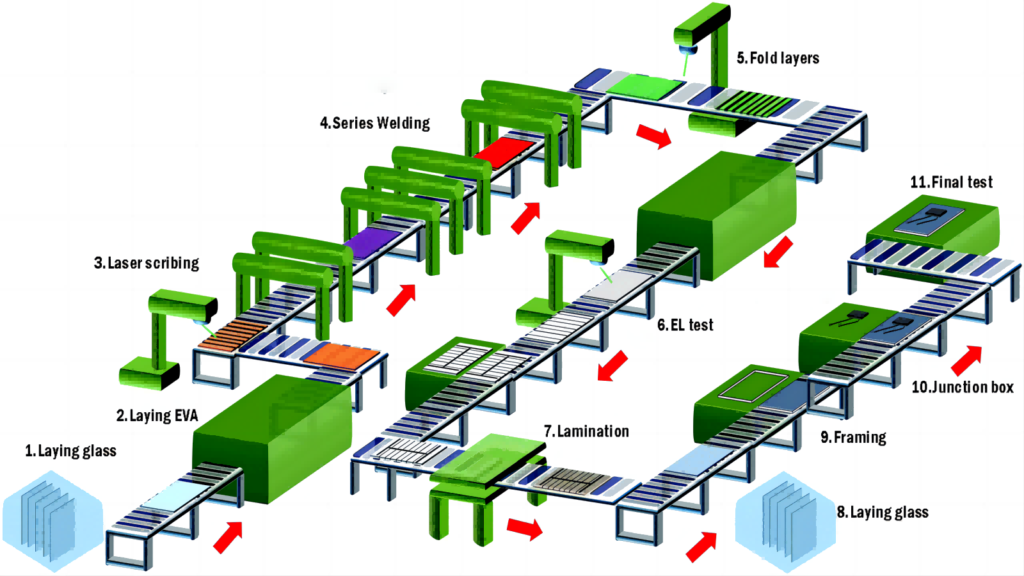
The process of making solar panels
Step 1: Half Cutting
Using a laser cutter to divide the cells in two and switching to small area cells in series is a good solution for reducing current losses and increasing module power. However, the module multiplies the number of connection points and places high demands on the production process. We will test the cut cells and only the ones that pass the test will proceed to the next step.
Step2:Welding
How do the individual cells connect to form a circuit? At high temperatures, solder tape connects the positive and negative poles of adjacent cells. The tape melts and cools quickly, creating a strong and permanent physical connection between the cells. This connection forms a string of cells. Here, we manually inspect it before moving on to the next step.
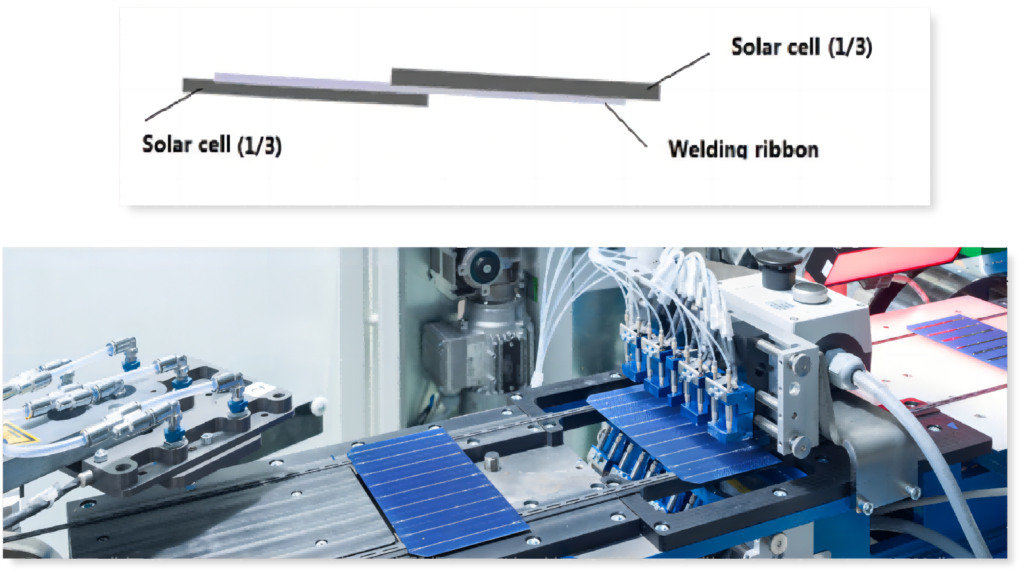
Step3:Layout
How do manufacturers build the internal structure of a PV module? First, arrange the cell strings on the PV glass covered with EVA. Next, solder the deflector strips to the solder strips on both sides of the cell strings to form the preliminary circuit. Additionally, the dispensing machine quickly fixes the circuit layout.
Note that to ensure the reliability of the solder strip, maintain a fixed distance of 2-5 mm between the horizontal and vertical directions of each cell in the assembly when attaching it above and below the cell surface. By implementing a reasonable design, we can project some of the irradiated light in the slit of the cells onto the surface of the battery again. This is achieved by reflecting the light twice using the back plate and glass. As a result, the output power of the PV panel can be increased.
The efficiency of PV conversion is determined by the arrangement of the cell, and the export of current is improved by determining how to lay the backplane. After dispensing, lay the EVA and backing plate in order on the cell. Pass the lead of the deflector strips through the holes on the backing plate, allowing the current to flow out of the cell along the lead.
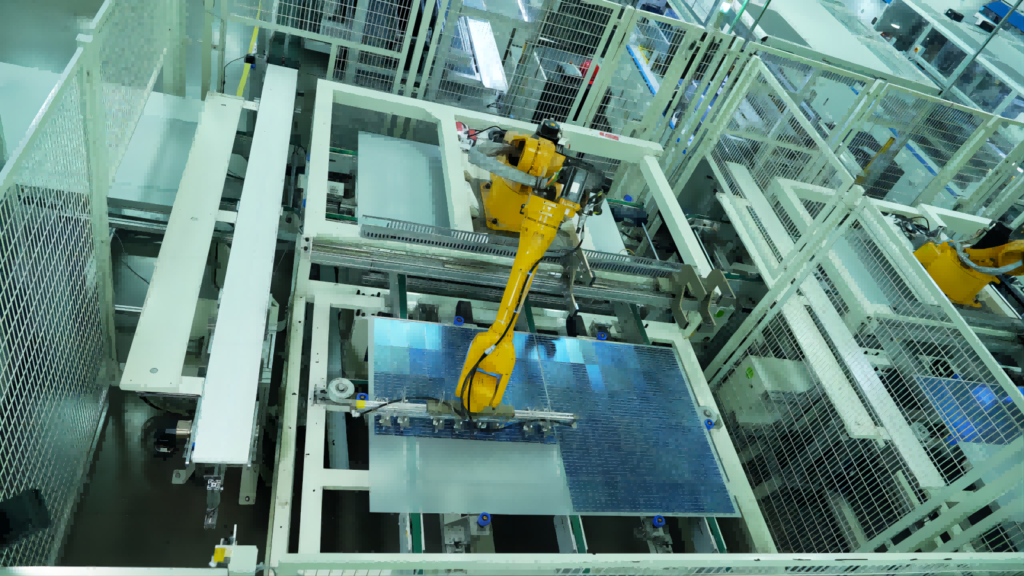
Step4:EL testing
The final process before lamination involves conducting EL testing, where the operator scans the module in the EL machine. We can easily spot dead or low power cells, short circuit cells, cracks, etc. If you spot any such error, send the module back to fix the error.

Step5:Lamination
During lamination, high temperatures tightly bond the glass, EVA, cells, and backsheet together to form the body of the module. Therefore, we need to make a final adjustment and conduct testing to ensure that the laminated components are more reliable.
We feed modules that pass the EI test into the laminator for final shaping. After laminating, leave the modules to cool down for 10-15 minutes until they reach room temperature.

Step6:Frame
To make the assembly process more precise, we need to cut the excess material at the edges to make the modules uniform in shape and size. The staff will check the appearance of the cells afterwards. Once you have everything in order, attach the cut aluminium frame tightly to the module using a sealant. The panel is fully protected and it prevents air, dust, and moisture from affecting the module.
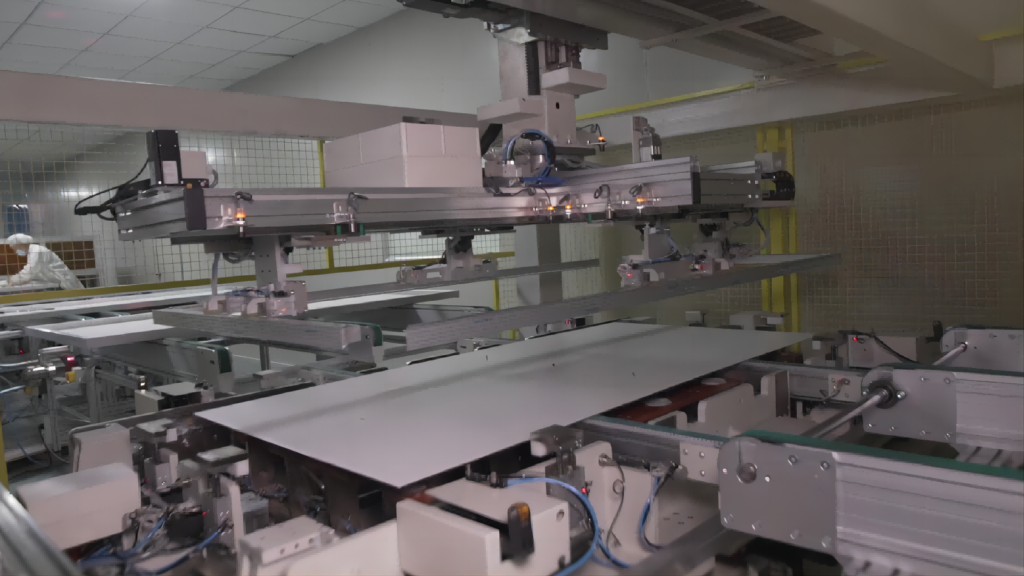
Step 7: Fix the junction box
The junction box is mounted on the deflector strips extending from the back plate. We attach the junction box to the module using sealant and soldering processes to ensure that current can flow out smoothly.
Step8:Solidify & Clean
After soldering, leave the module to solidify for 10-12 hours to allow the structure to completely dry and reach a stable condition. After the solidification process, you need to manually clean the module to remove dust, foreign objects, or spilled sealant to present the assembly in its best condition.
Step9:Module Testing
Once we manufacture the modules, we will move them on to the final 3 tests to ensure the quality of the finished product. We calibrate the output power of the cell, test its output characteristics, and determine the quality level of the component. First, we will carry out an insulation resistance test by passing DC current through the component for one. Firstly, we will carry out an insulation resistance test. We will pass DC current through the component for one minute. If the panel can endure the current, it will pass the test. Otherwise, it will fail. We test the component’s voltage withstand and insulation strength to ensure that it can withstand harsh natural conditions (such as lightning strikes) without getting damaged.
The power test is second. The staff will test the output current, voltage, power, etc. of the components and create label information. They will then stick the labels on the backboard for distinction.
Finally, we carry out the second EL test and visual inspection to minimise the detection error.
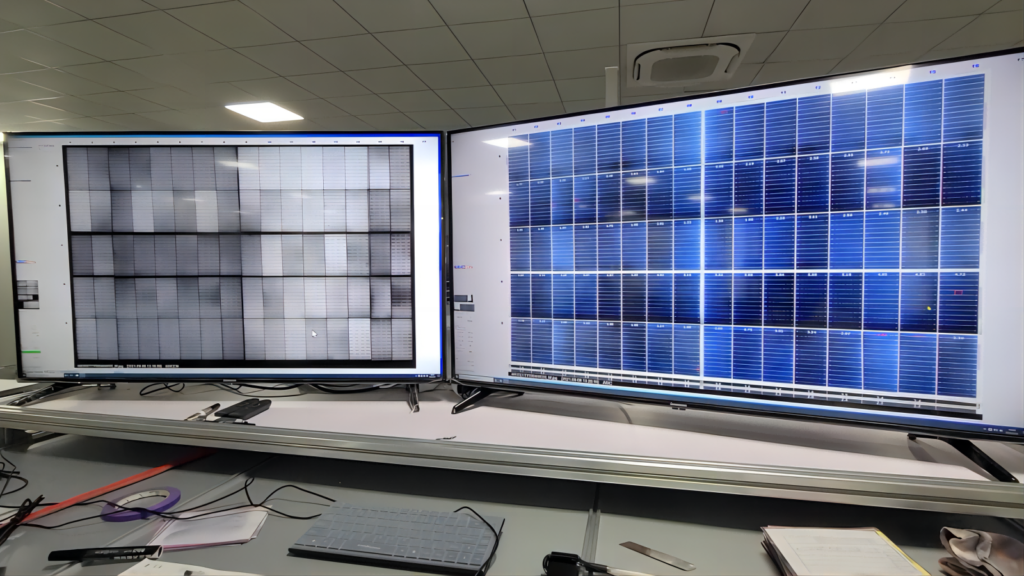
Step10:Packing
The staff will start packing the PV modules after completing the 3 final quality inspections. We will wrap cardboard around the 4 edges of each module to prevent accidents during transportation, in addition to packing them in cartons. We will wrap a film on the outside of the carton after completing the packing to better insulate air and moisture.
You can see that every Maysun solar panel, from the cells to the final delivery, goes through standardised steps and strict tests. We provide customers with a 15-year product warranty and a 25-year performance guarantee, allowing them to enjoy green and clean energy due to our insistence on product quality.
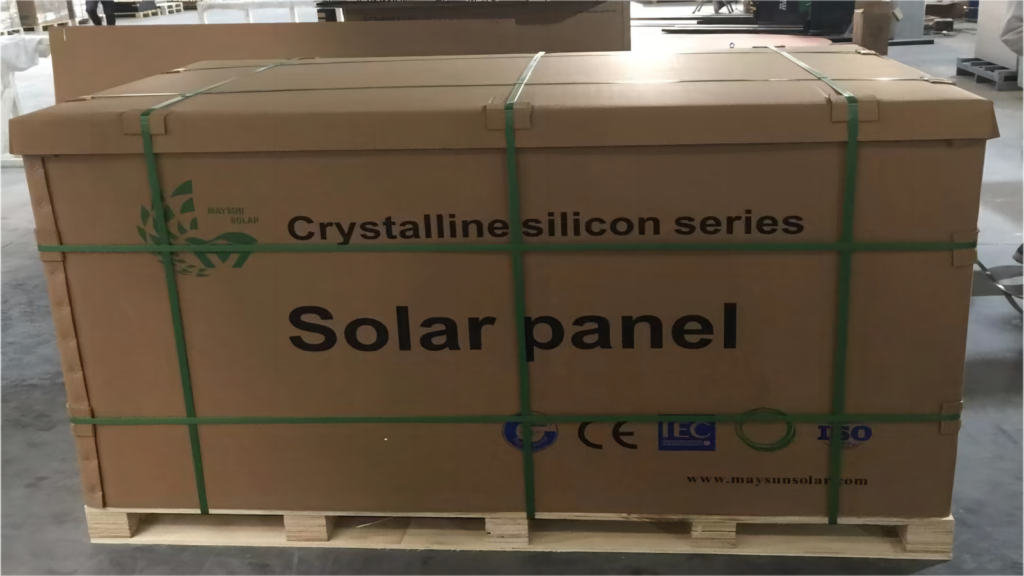
Below is an animated video produced by Maysun Solar describing how photovoltaic panels are manufactured, click on the video to learn more thoroughly!
How to ensure the high efficiency and high life span of solar panels?
1.High conversion efficiency, high-quality cells.
2.High-quality raw materials, such as: high cross-linking degree of EVA, high bonding strength of the encapsulant (neutral silicone resin adhesive), high transmittance high-strength toughened glass, and so on.
3.Reasonable encapsulation process.
4.The staff’s rigorous work style.
5.Reasonable and professional installation.
As the solar cell belongs to high-tech products, some details in the production process, some inconspicuous problems such as not wear gloves , should be uniformly coated reagents and scribbling, etc. are important factors affecting the quality of the product, so in addition to the development of a reasonable production process, the staff’s conscientiousness and rigour is very important.
Installation without gloves resulted in palm prints on the solar panels, which needed to be cleaned subsequently:
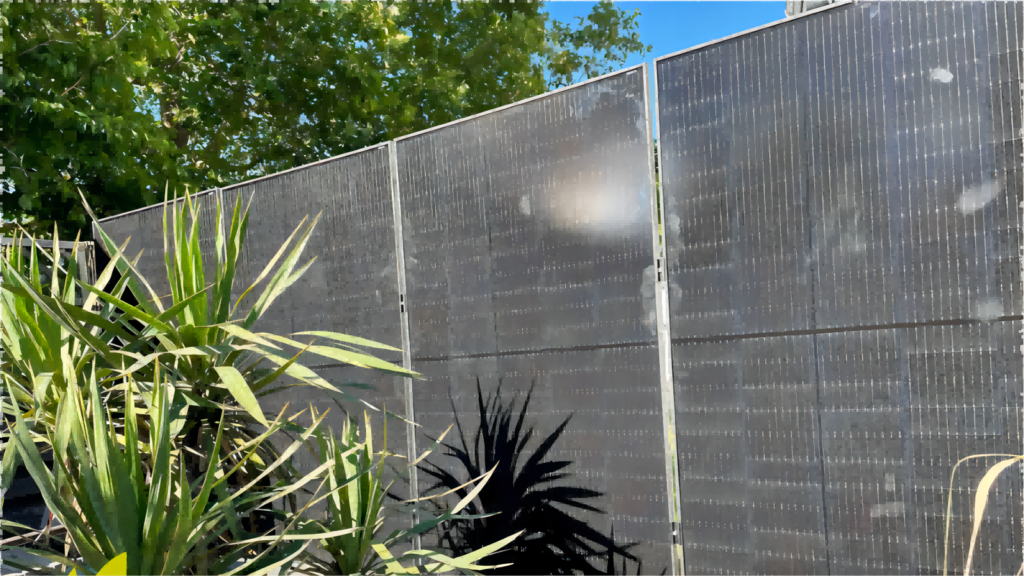
Maysun Solar’s solar panels all have high efficiency and longevity at a great price. Below is a picture of solar panel installation from our clients in Germany. Click on the picture to learn more about the product.
Since 2008, Maysun Solar has been dedicated to producing high-quality photovoltaic modules that contribute to combating climate change. Our advanced technology in IBC, HJT, TOPCon, and balcony solar panels ensures exceptional performance and reliability, capable of withstanding harsh weather conditions for long-term operation. We have established offices and warehouses in multiple countries and built lasting partnerships with top installers to provide comprehensive support. For the latest quotes or any inquiries related to photovoltaics, feel free to reach out to us—we’re here to help!
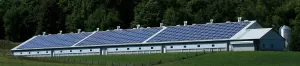
Empowering Factories with Solar Energy A Strategic Tool for Controlling Production Electricity Costs
Commercial and industrial solar is becoming a key solution for factories to reduce electricity costs and hedge against price fluctuations. This article systematically analyzes its deployment models, cost advantages, and sustainable value pathways.
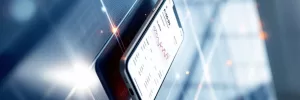
How Businesses Can Offset Carbon Taxes with Solar Power
This article analyzes the latest carbon tax policies and photovoltaic deduction strategies, helping European businesses legally reduce taxes, increase profits through solar investment, and achieve a win-win situation for both economy and environment.
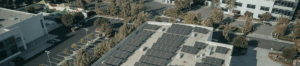
Forecast and Response: Seizing the Next Decade’s Growth Dividend in Europe’s Commercial and Industrial Photovoltaics Market
Maysun Solar analyzes the growth trends of commercial and industrial photovoltaics in Europe over the next ten years, from policies and ESG to technological innovation, helping companies seize the initiative in the energy transition.
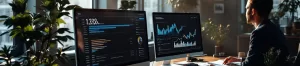
How to Calculate Solar System ROI and Optimize Long-Term Returns?
Solar power is becoming a key solution for businesses to reduce costs and improve efficiency. Accurately calculating ROI and optimizing long-term returns are essential to maximizing investment value.
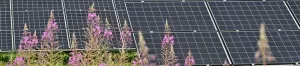
Will Agrivoltaics Affect Crop Growth?
Agrivoltaics combines solar energy and agriculture to reduce up to 700 tons of CO₂ per MW, improve water use, and boost crop growth for sustainable farming.
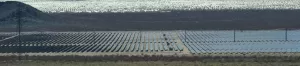
6.5 Billion Loss Hits Photovoltaics: Reshaping or Elimination?
In 2025, the photovoltaic market may see a turnaround as some companies take early action. A €6.5 billion loss is driving businesses to explore new growth areas like energy storage and hydrogen. Which giants will break through? Industry transformation is accelerating!