Intro:
Solar panel efficiency has reached unprecedented levels, yet the gradual reduction in the electricity output they can generate remains inevitable. Premium solar panels undergo degradation at an average rate of approximately 0.4% per annum, resulting in a decrease of about 12-15% in power output by the conclusion of their 25-30 year lifespan.
However, what factors contribute to the degradation of solar panels? What influences the pace at which solar panels degrade, and are there strategies to prolong their lifespan, thereby preventing their premature disposal as waste? The following content will answer these questions in detail.
Content:
1.LID and recommendations to minimise the impact of LID
2.PID and recommendations to minimise the impact of PID
3.Natural ageing of solar panels and suggestions
4.Micro-cracks and hot spots of solar panels and suggestions
The degradation of solar panel includes LID, PID, natural degradation, microcracks and hot spot effect. As the solar panels themselves are used over time, the components naturally age and become less efficient. The primary cause of solar panel degradation is the natural wear and tear that occurs over time due to exposure to UV rays and adverse weather conditions. The rate of degradation is typically covered by a panel’s performance warranty. In addition to this, the initial exposure of solar panels to sunlight can cause LID, the high pressure, high temperature and increased humidity can cause PID, improper handling and mounting of solar panels can lead to the appearance of microcracks, and shadowing of the mounting location can cause the hot spot effect. We’ll go into more detail below.
LID (Light-induced Degradation)
LID (Light-Induced Degradation) has various forms of mechanical and chemical degradation stem from the panel’s exposure to light, which includes: BO-LID, LeTID and UVID. It serves as a key reliability parameter in the realm of photovoltaic modules and it encompasses primarily three distinct categories: Boron-Oxygen compound light degradation (BO-LID), light and elevated temperature-induced degradation (LeTID), and surface passivation degradation induced by ultraviolet exposure (UVID).
BO-LID (Boron-Oxygen Compound Light Degradation)
BO-LID, or Boron-Oxygen compound light degradation, is a crucial aspect of solar panel performance. In the realm of LID (Light-Induced Degradation), BO-LID stands out as the primary contributor to the light-induced degradation observed in crystalline silicon cells. When photovoltaic modules are first exposed to sunlight, BO-LID swiftly takes effect, causing a rapid reduction in the rated wattage (Wp) output of the panels. This initial decrease, typically ranging from 2% to 3%, occurs within a mere few hundred hours of operation, with the most significant impact usually noticeable during the initial year of use.
The noteworthy aspect of BO-LID is that it often reaches a saturation point relatively quickly, typically within days or weeks. The encouraging news is that mitigating or even eliminating the effects of BO-LID is possible. This can be achieved through strategies such as modifying dopants, such as the introduction of Gallium, or enhancing passivation techniques. These measures play a pivotal role in preserving the long-term performance and efficiency of solar panels.
Following this initial stabilization phase, the rate of LID undergoes a substantial decrease, reaching levels as low as 0.3% to 0.5% per year for the subsequent 25+ years. Notably, high-performance modules from Maysun Solar, such as IBC, can exhibit LID rates as low as 0.4% per year. This excellent performance is due to proven production techniques and high quality materials.
Fortunately, most manufacturers tend to slightly over-specify the panel’s power rating by up to 5%. This allowance accounts for minor cell imbalances and offsets some of the initial degradation, thereby ensuring the accuracy of the rated panel power (Wp). To illustrate, a 350 Watt panel may initially produce up to 5% more power, potentially reaching up to 368 Watts for a brief period. Nevertheless, this slight overproduction is typically of short duration and might remain imperceptible unless the panels operate under ideal (STC) conditions. The manufacturer’s performance warranty comprehensively outlines the rate of LID and the expected performance decline over the 25-year warranty period.
UVID (UV Light-induced Degradation):
UVID concerns the potential deterioration in the performance of solar modules after extended exposure to ultraviolet radiation. The initial exposure to sunlight causes the crystalline silicon oxide on the panel’s surface to develop a layer of boron dioxide, which reduces its efficiency. This degradation is primarily associated with the materials employed in solar cells, particularly those related to photoelectric conversion. Prolonged exposure to UV radiation can induce chemical reactions or material breakdown within the cells, resulting in performance degradation. This often manifests as reduced efficiency and power output. To address the effects of UVID, manufacturers typically opt for materials with high UV stability, enhance the module’s encapsulation materials to provide improved protection, and subject the modules to UV exposure tests to assess their resilience.
LeTID (Light and Elevated Temperature Induced Degradation):
LeTID (Light and Elevated Temperature Induced Degradation): LeTID represents a decline in performance induced by elevated temperatures, primarily linked to materials and imperfections within solar cells. When subjected to high temperatures and radiation, defects within the cell can multiply, causing charge recombination and heightened resistance, resulting in a decrease in the cell’s performance. LeTID resembles LID in some respects; however, the losses attributed to LeTID have been documented to reach levels as high as 6% within the first year. If not adequately addressed by the manufacturer, this could result in subpar performance and potentially lead to warranty claims.
LeTID effects are typically discernible during real-world module operation, rather than laboratory conditions. To counteract LeTID effects, manufacturers frequently enhance material selection, refine production procedures, perform thermal stability assessments, and assess cell performance at elevated temperatures to ensure consistent module performance.
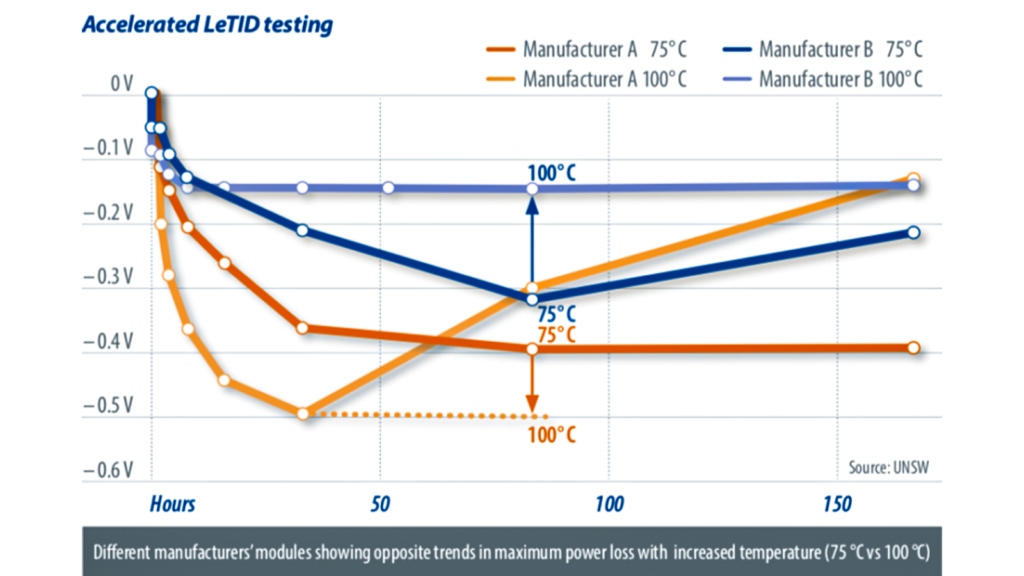
Suggestion:
Panel Selection: Invest in panels using high-purity N-type silicon cell substrates for lower LID rates. Maysun Solar’s HJT solar panels are a great choice! HJT cells are immune to the LID effect because the substrate is usually N-type monocrystalline silicon, which is phosphorus doped and does not have the boron-oxygen composite, boron-iron composite, etc. found in P-type crystalline silicon. HJT solar modules have a 30-year degradation of no more than 12.6%, resulting in more stable power generation over the life of the solar module. They have high flexibility, high cell efficiency, high bifacial rate and low attenuation.
Over-Specification: Panels often have power allowances to compensate for initial degradation.
UV Stability: Manufacturers should subject modules to UV exposure tests to ensure resilience.
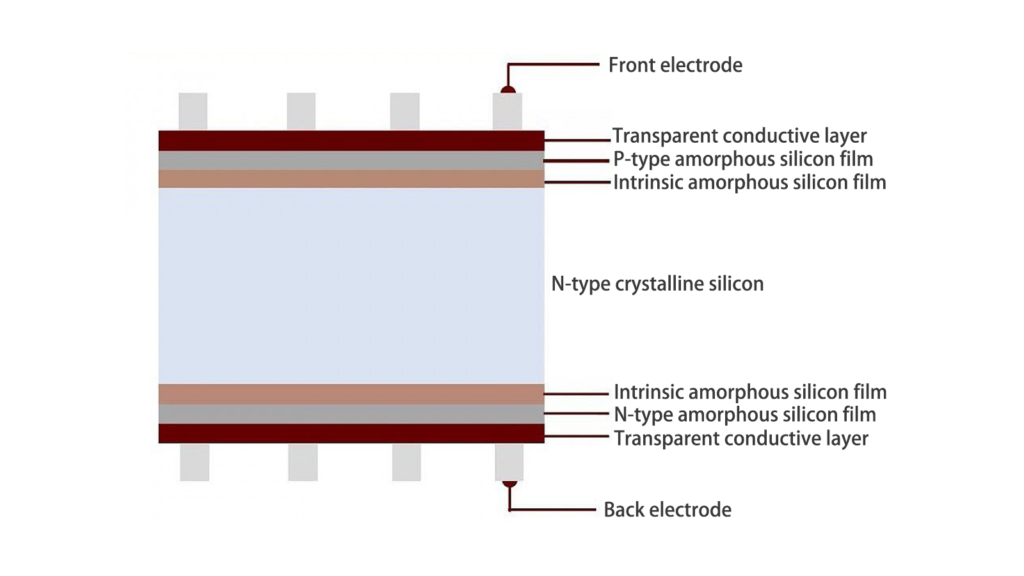
PID (Potential-Induced Degradation)
Potential-Induced Degradation, or PID, is a type of solar panel deterioration that typically becomes noticeable after 4 to 10 years of usage. It results from factors such as high voltage, elevated temperatures, and increased humidity. Essentially, PID involves the leakage of voltage from the solar cells to the frame of the solar panel, leading to a reduction in power output. Unfortunately, this issue may not be immediately discernible, but it tends to worsen gradually over time. Diagnosing PID can be challenging without the use of specialized IV curve testers and proper training. However, one early indicator might be an unusually low string voltage or current. You can find more information on diagnosing PID problems in our blog.
The majority of residential rooftop solar arrays operate within the 300 to 600-volt range, and PID is more prominent when higher string voltages are involved. Therefore, the more panels connected in a string, the higher the likelihood of PID occurrence. Large-scale solar farms, on the other hand, often function within the 1000 to 1500-volt range, significantly increasing the risk of PID. Fortunately, some advanced large-scale solar inverters can counteract PID effects, if detected, by running a very small reverse current overnight.
In severe cases where PID issues are left unaddressed for 10 or more years, power output can be severely impacted, resulting in potential losses of up to 50%. However, many of the leading solar panel manufacturers have substantially mitigated the risk of PID by employing high-quality materials and subjecting their products to rigorous testing. Nevertheless, PID remains a persistent issue, as underscored by the latest test results from the independent testing institution PVEL.
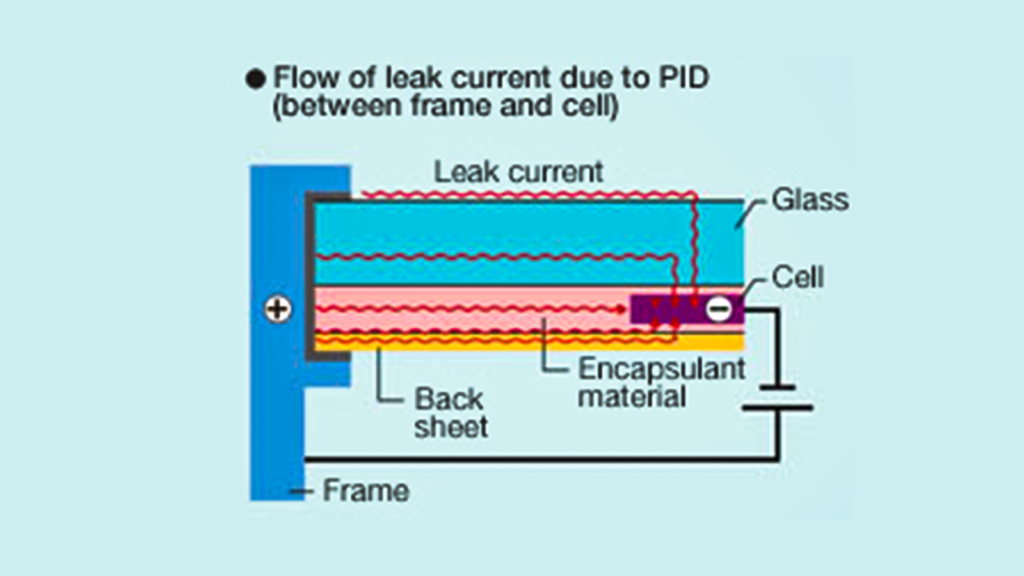
Suggestion:
Through extensive research and long-term experimentation, Maysun’s team of experts has identified effective approaches to mitigate Potential-Induced Degradation (PID). These key methods primarily include:
1.Grounding the negative terminal of serial components or applying a positive voltage between the module and the ground, especially during the evening hours.
2.Improving the durability and quality of the EVA film while optimizing the encapsulation process.
3.Implementing modifications to the cell’s emitter and the Silicon Nitride (SiN) anti-reflection layer.
Maysun’s innovative HJT solar cell boasts exceptional anti-PID performance. This is attributed to its TCO (Transparent Conductive Oxide) thin film layer, which possesses conductive properties that effectively prevent surface charge polarization. By doing so, this advanced technology structurally mitigates the risks associated with PID degradation.
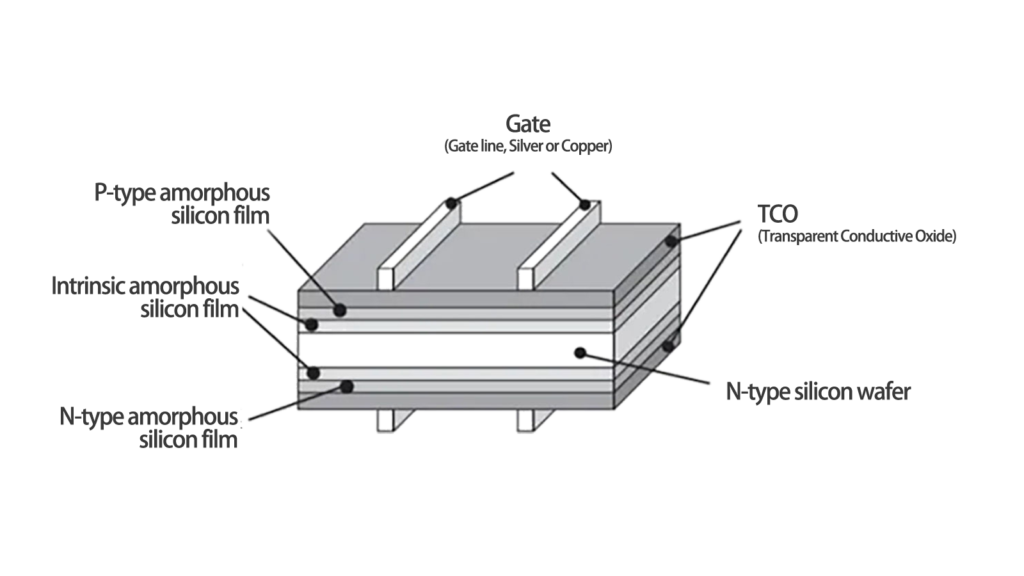
Natural Ageing Degradation of Solar Panels
Aside from the well-known PID and LID effects, solar panels can encounter even more severe issues stemming from the deterioration of the encapsulant and protective layers, which are intended to shield the cells from environmental factors. One of the most prevalent issues is back-sheet failure. While the front glass sheet provides protection against rain, hail, dirt, and debris, the white or black plastic back-sheet serves to safeguard the rear side of the cells from water, humidity, and abrasions. However, subpar material choices and inadequate quality control measures can lead to the breakdown, cracking, or degradation of either the encapsulant or the rear protective back-sheet due to UV radiation. This deterioration can subsequently result in more critical problems like moisture infiltration, corrosion, and electrical leakage. As time goes by, their performance can diminish, resulting in reduced energy production. Here, we analyze the primary factors that influence the durability of these panels:
Encapsulant Discoloration:
Exposure to prolonged UV radiation can result in the discoloration of the encapsulant material within solar panels. This not only affects the aesthetics of the panels but also interferes with their light absorption capabilities. The encapsulant is responsible for protecting the sensitive solar cells from external elements, and when it discolors, it hinders the passage of light to the cells, reducing the overall conversion efficiency of the panels. To mitigate this, high-quality UV-stable encapsulant materials are used, and regular cleaning and maintenance can help extend their lifespan.
Typically, EVA (Ethylene-Vinyl Scetate ) ,POE(Polyethylene) and EPE (EVA+POE+EVA) serve as encapsulant materials to shield solar cells from external environmental factors. These encapsulant materials typically maintain their integrity for approximately 25-30 years. Among them, although EVA is widely used because of its low cost and high processability, his shortcomings are being discovered by more and more people. Nowadays, POE and EPE are used more and more, because although these two materials are costly and difficult to produce, they have excellent PID resistance, high resistivity, high water vapour barrier, stable and reliable low-temperature resistance and yellowing resistance.
Backsheet Degradation:
Backsheets are usually constructed from materials like polyvinyl fluoride (Tedlar) or polyester (PET) to safeguard the backside of solar cells against moisture and other environmental elements. The lifespan of the backsheet typically aligns with the expected lifespan of the solar panels, around 25-30 years. Over time, especially in regions with high temperatures and humidity, the backsheet’s resistance to moisture may deteriorate. This degradation increases the risk of encapsulant hydrolysis, which can lead to cell corrosion. The backsheet is a vital component of solar panels as it provides protection against environmental factors, making it crucial to maintain its integrity. Using durable, moisture-resistant backsheets and providing proper ventilation under the panels can help reduce backsheet degradation and, subsequently, encapsulant hydrolysis.
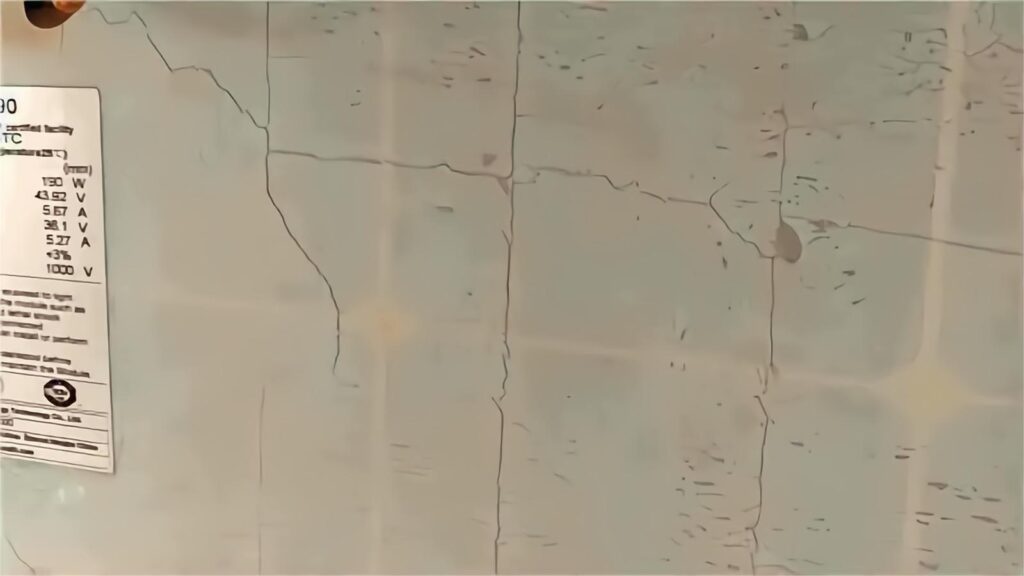
Backsheets that meet the requirements of PERC cell modules are chosen based on whether they are of N-type or N-type TOPCon. To align with low water vapor transmission (≤0.15 grams per square meter) requirements, a specific type of backsheet is selected. Typically, the choice involves matching EVA film with POE and EPE, with a preference for the double-glass process. However, for HJT cells with higher light transmission demands, standard backsheets may not suffice, leading to the selection of double-glass modules with zero water vapor transmission.
In cases involving N-type TOPCon and HJT technologies, there is also the option to consider PAPF (aluminum foil-containing) backsheets, although these are used in limited quantities. It’s important to be aware that such choices come with potential leakage risks and may lack comprehensive validation.
Solar Cell Efficiency Decline:
Solar cells are typically made of monocrystalline silicon, polycrystalline silicon, or other semiconductor materials. They are the critical component of solar panels and can operate effectively for several decades. Most manufacturers offer a performance warranty of at least 25 years. Continuous operation under challenging environmental conditions can induce changes in the material properties of solar cells, resulting in a reduction in efficiency and power output. Solar cells are at the heart of any solar panel, and their optimal performance is essential for energy production. To counteract cell efficiency decline, manufacturers are constantly improving cell technologies. Some advanced panels are designed with materials that are less prone to degradation, such as high-purity silicon. Proper maintenance, including keeping the panels clean and shading-free, can also help preserve cell efficiency.
Glass: Glass covers the solar cells, providing protection against environmental damage and structural support. The glass commonly used in solar panels is either semi-tempered glass or fully tempered glass, with a typical lifespan that aligns with the solar panels, approximately 25-30 years. Single-glass solar panel adopts fully tempered 3.2mm glass, glass-glass solar panel adopts semi-tempered 2.0mm glass or semi-tempered 1.6mm glass.
Single-glass solar panels often use fully tempered glass, because fully tempered glass has high mechanical strength against impact and is resistant to high and low temperatures. However, although fully tempered glass exhibits strong impact resistance, it is not suitable for use in glass-glass solar panels. This is because fully tempered glass has poor flatness, high stress, and is not conducive to the lamination production process of the solar modules, resulting in low yields. The use of semi-tempered glass significantly reduces the occurrence of these issues. While semi-tempered glass may have lower impact resistance and heat resistance, it offers excellent flatness, low-stress, and boasts high yields.
If we want to install solar panels, we need to pay attention to the correct installation method, regular inspection and maintenance, reasonable and safe installation location, but also need to choose high-quality solar panels. For instance, Maysun’s IBC solar panels are backed by a 25-year warranty for both power output and product quality. They guarantee only a 1.5% efficiency decrease in the first year and a mere 0.4% annual linear reduction thereafter, ensuring consistent benefits for users throughout the panel’s lifespan.
Micro-Cracks and Hot Spots
Micro-cracks can develop over time, leading to the formation of hot spots within solar panels. These issues may result from mishandling during installation, extreme wind loads, or transportation damage. Hot spots are areas where excess heat is generated, causing potential damage to the panels.
Micro-Cracks
The majority of modern solar panels are constructed using a sequence of solar cells comprised of ultra-thin crystalline silicon wafers. These wafers typically measure around 0.16mm in thickness, approximately twice the width of a human hair. Naturally, both the wafers and cells are relatively fragile and are susceptible to cracking or fracturing when exposed to high mechanical pressures, such as mishandling during installation, extreme wind loads, or large hail. It’s important to mention that not all cells are brittle; high-performance IBC cells from reputable brands are notably more robust due to the extensive array of back-contacts that reinforce the cell. Modern panels often incorporate features like half-cut cells, which are more resistant to micro-cracks and hot spots, and shingled configurations that spread the heat load more evenly.
Any unusual loads or stresses, such as individuals walking on solar panels during installation or maintenance, can generate micro-cracks, which may evolve into hot spots over time and eventually result in panel failure. Micro-cracks can also develop during transportation, due to impacts, dropping, or rough handling.
Detecting micro-cracks can be challenging, and they are frequently imperceptible initially. On older panels, small fractures within the solar cells may become visible, resembling snail trails on the cell’s surface. These fractures don’t consistently pose a significant issue, and the panel may continue to perform well for many years, even with multiple cracked cells. However, micro-cracks can escalate into a more serious concern as they raise internal resistance and interrupt the current flow, resulting in a hot spot or hot cell. This is especially problematic when a micro-crack is extensive or spans the entire cell.
Fortunately, most contemporary solar panels now incorporate half-cut cells with multiple busbars, substantially mitigating the adverse effects of micro-cracks. Additionally, shingled solar panels are generally immune to micro-cracks due to their distinctive overlapping configuration.
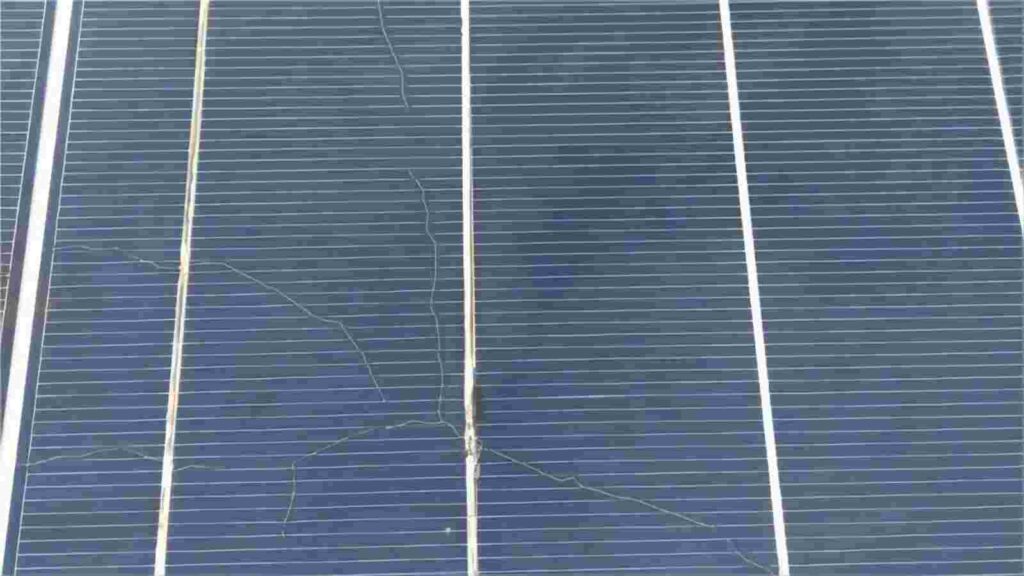
Suggestion:
Professional Installation: Opt for experienced and well-trained installers who can handle solar panels with care during installation. Improper handling can induce micro-cracks. Ensure that the panels are securely mounted to minimize mechanical stress.
Half-Cut Cells: Choose solar panels equipped with half-cut cells and multiple busbars. These cells are more robust and less susceptible to micro-cracking, as they distribute stress more effectively.
Shingled Solar Panels: Shingled solar panels are designed with overlapping cells, reducing the risk of micro-cracks. They provide enhanced durability and longevity.
Regular Inspections: Implement a routine inspection schedule using thermal imaging cameras. These inspections can detect micro-cracks that may not be visible to the naked eye, allowing for early intervention.
Optimal Installation Practices: Ensure the panels are installed at the correct angle and firmly secured to prevent mechanical stress that can lead to micro-cracks.
High-Quality Materials: Select solar panels from reputable manufacturers that employ quality materials. These panels are better equipped to withstand environmental factors and mechanical stresses, minimizing the risk of micro-cracks.
Shade Management: Mitigate shading from nearby structures or objects. Persistent shading can lead to the gradual formation of hot spots, which are associated with micro-crack development.
Hot Spots
Solar cells produce an electric current that flows through interconnected cells. When this flow is disrupted by an internal fault or severe micro-cracks, increased resistance generates heat. This, in turn, amplifies resistance further, resulting in the formation of a hot spot. In severe cases, a hot spot can even cause damage to the cell. For in-depth information, you can refer to a comprehensive article of Maysun Solar, which delves into the mechanisms of micro-cracking and how new panel designs and innovations can reduce the likelihood of micro-crack development.
Both hot spots and micro-cracks are not always visible to the naked eye. Often, the sole way to determine whether a solar panel is compromised is by using a specialized thermal imaging camera, which highlights temperature disparities among various cells. It’s essential to note that persistent shading from obstacles on rooftops can, in some instances, lead to the gradual formation of hot spots over several years, primarily due to the reverse current effect of shaded cells.
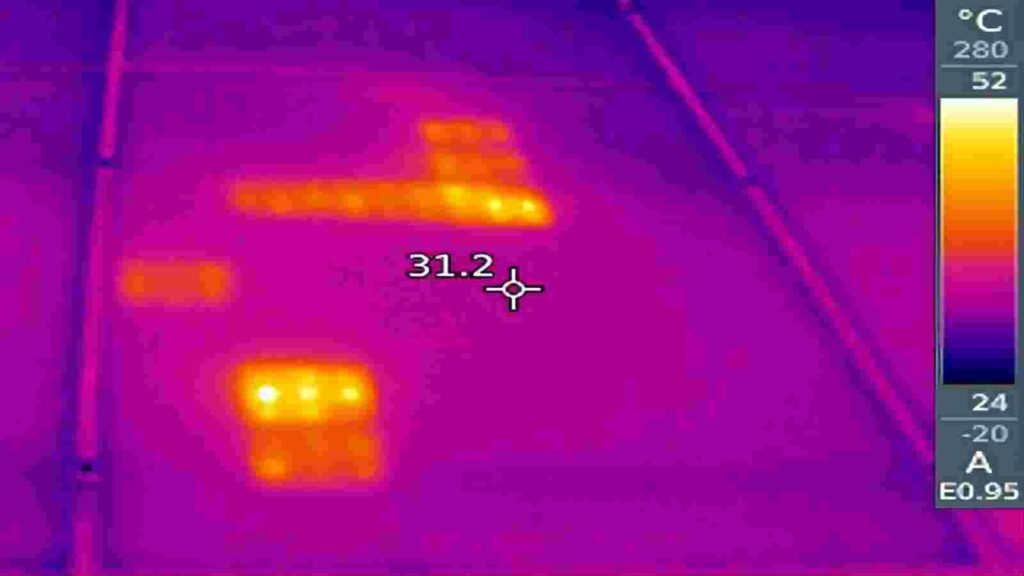
Increased temperatures resulting from hot spots can present fire hazards and other safety concerns. To address the hot spot issue, Maysun Solar has incorporated MOS bypass switches into their Venusun series solar panels, replacing conventional bypass diodes. These switches provide rapid responses to changing light conditions, adjusting promptly to minimize the effects of shading on panel performance. Below is a picture of a Venusun All Black 410W solar panel installation from Maysun’s Belgian installer, click on the picture to see the product details!
Maysun’s IBC solar panels have positive and negative metal electrodes on the backside that flow normally when shaded. With no resistance on the front side, the risk of hot spots is greatly reduced.
In addition to choosing quality solar panels, we also need to pay attention to the following suggestions:
Reduced shading: Conducting a thorough shade analysis is an essential step in the strategy to prevent hot spots. This analysis helps identify and mitigate potential shadow and shading problems from nearby objects or structures, further reducing the chances of hot spot occurrence.
Routine Cleaning: Consistent panel maintenance, involving the regular removal of dust and debris, plays a pivotal role in enhancing efficient heat dissipation and, as a result, in preventing the formation of hot spots. This upkeep helps maintain a clear and unobstructed panel surface.
Inverter Sizing: Properly sizing the inverter is critical to prevent voltage instability stemming from oversized inverters or the underutilization associated with undersized ones. Voltage stability is vital in minimizing hot spot risks.
Temperature Monitoring: Implementing temperature monitoring systems enables the early detection of temperature variations within the panels. This proactive approach is effective in preventing the formation of hot spots by identifying potential issues promptly.
Advanced Panel Designs: Opting for panels with advanced designs, such as half-cut cells or shingled configurations, offers the advantage of even distribution of electrical current. This design choice significantly reduces the risk of localized hot spots.
Heat Dissipation Design: The design of solar panels should allow for effective heat dissipation to prevent overheating during operation. This can be achieved by leaving sufficient space around the panels to allow for airflow and efficient cooling. Additionally, ensuring proper backsheet and frame design facilitates the dissipation of heat, reducing the internal temperature of the panels. This, in turn, helps to minimize the risk of hot spot formation.
Current Matching: To reduce uneven current distribution, it is essential to ensure that the current characteristics of all solar cells match. This can be accomplished through precise selection and matching of solar cells to ensure they have similar current outputs. Current matching minimizes current fluctuations within the entire solar panel, thereby decreasing the likelihood of hot spot formation. This process also enhances the overall efficiency and performance of the system.
For more information on the hot spot effect, click the button below to read the article:
Since 2008, Maysun Solar has been a dedicated producer of top-tier photovoltaic modules. Explore our extensive range of solar panels, available in full black, black frame, silver, and glass-glass variants, featuring cutting-edge technologies like half-cut, MBB, IBC, and Shingled. Our panels deliver exceptional performance and boast elegant designs that seamlessly integrate with any architectural style.
Maysun Solar has successfully established a global presence, with offices, warehouses, and long-term partnerships with exceptional installers in various countries. For the latest module quotations or any PV-related inquiries, please do not hesitate to reach out to us. We are enthusiastic about the opportunity to assist you.
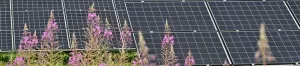
Will Agrivoltaics Affect Crop Growth?
Agrivoltaics combines solar energy and agriculture to reduce up to 700 tons of CO₂ per MW, improve water use, and boost crop growth for sustainable farming.
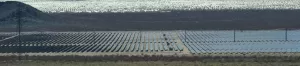
6.5 Billion Loss Hits Photovoltaics: Reshaping or Elimination?
In 2025, the photovoltaic market may see a turnaround as some companies take early action. A €6.5 billion loss is driving businesses to explore new growth areas like energy storage and hydrogen. Which giants will break through? Industry transformation is accelerating!
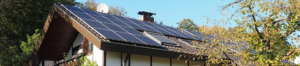
What’s New in Solar Energy (March 2025)
March’s solar news highlights include rooftop solar meeting two-thirds of global demand, China’s market reforms potentially boosting solar demand and module prices, France revising solar targets in PPE 3, and challenges in Europe with declining capture rates and price volatility.
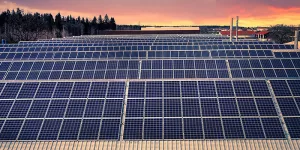
Zero-Investment Solar Projects: How to Earn Passive Income Through Rooftop Leasing?
Monetize your idle rooftop and earn stable annual rent! With the photovoltaic rooftop leasing model, businesses can generate long-term revenue without investment, reduce operating costs, and achieve a green transition.
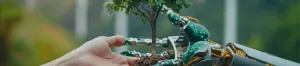
How to Optimize Photovoltaic Power Plant Operations with AI and Big Data
This article explores three methods of using AI to enhance power generation revenue and reduce operation and maintenance costs in intelligent photovoltaic operations.

Solar Module Costs May Rise by 10% in 2026! In-Depth Analysis of CBAM’s Impact on the Industry
Table of Contents Introduction to CBAM 1. Why Did the EU Introduce CBAM? As the challenges posed by global climate change intensify, governments worldwide are accelerating their efforts to achieve carbon neutrality. The European Union, a leader in global carbon reduction initiatives, introduced